HISTORY OF TECHNOLOGY
Prehistory
The use of tools
It is a commonplace that humans are distinguished from other creatures by a technological ability, and man has often been described as a tool-using animal. The distinction is not entirely valid. Some animals do use tools. Chimpanzees are the most often quoted example, stripping a twig to plunge it into an anthill and then eating the tasty termites which cling to the end of it.
A more modern example of tool-using is that of crows living in a walnut avenue in the Japanese town of Sendai. The walnuts are too hard to crack. So the crows have taken to dropping them on a pedestrian crossing where they are crushed by the passing traffic. When it is the pedestrians' turn, the crows fly in to bear off the fragments.
A more modern example of tool-using is that of crows living in a walnut avenue in the Japanese town of Sendai. The walnuts are too hard to crack. So the crows have taken to dropping them on a pedestrian crossing where they are crushed by the passing traffic. When it is the pedestrians' turn, the crows fly in to bear off the fragments.
But there is a difference between using a tool which comes to hand, however improbably, and fashioning one for a purpose. Shaping a tool for cutting or scraping (two basic and useful functions) is a difficult task. Such a tool must be made of a hard material, and the hardest material easily available on the surface of the earth is stone. But how does one shape a stone without tools?
The history of human technology begins with the discovery of how to give stone a cutting edge. The type of stone found most suitable for the purpose is flint.
The history of human technology begins with the discovery of how to give stone a cutting edge. The type of stone found most suitable for the purpose is flint.
Stone tools: from 2.5 million years ago
The human discovery that round nodules of flint can be split and chipped to form a sharp edge is extremely ancient. Tools made in this way have been found in Africa from about 2.5 million years ago (the earliest known examples have been discovered at Gona, in the Awash Valley in Ethiopia). Gradually, over the millennia, in an extremely slow version of an industrial revolution, new and improved techniques are developed for striking off slivers of stone.
Variations in the flints found with fossil remains (differing both in the method by which flakes are chipped from the core, and in the range of shapes created) are used by anthropologists as one way of assigning human skeletal remains to specific groups or divisions of the Stone Age.
Variations in the flints found with fossil remains (differing both in the method by which flakes are chipped from the core, and in the range of shapes created) are used by anthropologists as one way of assigning human skeletal remains to specific groups or divisions of the Stone Age.
In the earliest periods a sgle tool is usually made from the core of the flint, resulting in an instrument that can be used in a fairly rough manner for either cutting or scraping. Hundreds of thousands of years later, craftsmen have become skilled at forming the flakes themselves into implements of various kinds, producing specialist tools for cutting, scraping, gouging or boring, as well as sharp points for arrow and spear heads.
These sophisticated stone tools, in their turn, make it possible to carve materials such as antler or bone to create even sharper points, or more complex shapes (such as hooks or needles).
These sophisticated stone tools, in their turn, make it possible to carve materials such as antler or bone to create even sharper points, or more complex shapes (such as hooks or needles).
The predominant use of stone as the material for tools has caused this period to be known as the Stone Age. It represents by far the greatest part of human history, spanning more than 2 million years to a time only a few thousand years ago.
The Stone Age includes all human development up to the point which one might describe as the beginning of civlization. It has inevitably proved too loose a term and has been much subdivided (see Divisions of the Stone Age).
The Stone Age includes all human development up to the point which one might describe as the beginning of civlization. It has inevitably proved too loose a term and has been much subdivided (see Divisions of the Stone Age).
Fire: from 500000 years ago
An event of crucial importance in the development of technology is man's taming of Fire. This probably happens some 500,000 years ago in China, where the caves occupied by Peking man contain what appear to be hearths. Some experts believe there is evidence of the use of Fire much earlier in south Africa.
It will be many millennia before Fire is adapted to any purpose other than for warmth and for roasting meat and root vegetables. But more than 250,000 years ago hunters realize that the sharpened point of a wooden spear can be Hardened by charring it in embers.
It will be many millennia before Fire is adapted to any purpose other than for warmth and for roasting meat and root vegetables. But more than 250,000 years ago hunters realize that the sharpened point of a wooden spear can be Hardened by charring it in embers.
Neolithic technology: from 8000 BC
The technological potential of fire is not discovered until well into the neolithic period. Pottery, fired in a primitive kiln, is known from about 6500 BC. The Smelting and casting of metal require considerably higher temperatures and are not attempted until much later, from about 4000 BC. The introduction of copper, and then bronze, brings to an end the neolithic period.
Other basic technologies, not requiring fire, are well established in neolithic times. Textiles feature almost as early as Pottery. Weights designed for spinning are common in neolithic sites, and fragments of fine woven cloth survive in graves at Catal huyuk from as early as 5800 BC.
Other basic technologies, not requiring fire, are well established in neolithic times. Textiles feature almost as early as Pottery. Weights designed for spinning are common in neolithic sites, and fragments of fine woven cloth survive in graves at Catal huyuk from as early as 5800 BC.
Bricks: from 8000 BC
An innovation in the neolithic period is the use of bricks. In their simplest form (still familiar today in many hot regions), bricks are shaped by pressing mud or clay into a mould. The damp blocks are then left to bake hard in the sun. Bricks of this kind are known in Jericho from about 8000 BC.
The more durable type of brick, baked in a kiln, is an offshoot of the potter's technology. Kiln bricks are widely used in the two earliest civilizations, in Mesopotamia and Egypt, often to provide the outer surface of walls on an inner core of sun-dried brick.
The more durable type of brick, baked in a kiln, is an offshoot of the potter's technology. Kiln bricks are widely used in the two earliest civilizations, in Mesopotamia and Egypt, often to provide the outer surface of walls on an inner core of sun-dried brick.
Spinning: from 8000 BC
The spindle develops naturally from the process of twisting fibres into a thread by hand. The spun thread must be stored, and the easiest way is to wind it onto a stick. This means that the stick is also attached to the unfinished thread (the fibres which are still being twisted). The stick must therefore twist with the fibres.
Instead of being an encumbrance, this can be turned to advantage. If the stick is given greater weight, by attaching to it a lump of clay or a stone, its momentum will help in spinning the thread.
Instead of being an encumbrance, this can be turned to advantage. If the stick is given greater weight, by attaching to it a lump of clay or a stone, its momentum will help in spinning the thread.
The thread can be turned into fabric in either of two ways. One of them links a continuous length of thread in rows of interconnected loops. This is Knitting, which can create garments of any shape.
The other method, going back to at least 5800 BC, uses the thread in a rectangular criss-cross pattern to produce flat cloth. The vertical threads are stretched taut to form a grille; the horizontal threads are then interwoven between them. This is the process for all textiles of cotton, linen, silk or wool. It also produces tapestry. It makes the cloth which is decorated in embroidery. When loops are inserted, it gives the soft pile of rugs and carpets. All these involve the basic craft of weaving.
The other method, going back to at least 5800 BC, uses the thread in a rectangular criss-cross pattern to produce flat cloth. The vertical threads are stretched taut to form a grille; the horizontal threads are then interwoven between them. This is the process for all textiles of cotton, linen, silk or wool. It also produces tapestry. It makes the cloth which is decorated in embroidery. When loops are inserted, it gives the soft pile of rugs and carpets. All these involve the basic craft of weaving.
So the spindle acquires its two characteristics. It is a bobbin, on to which the spun thread is wound; and it is a flywheel, prolonging the spinning motion which creates the thread.
The spinner uses one hand to draw out the fibres from the bundle of wool, cotton or flax, thus extending the half-spun thread to which the spindle is attached. The other hand gives a rotating flick to the spindle whenever it begins to lose impetus. Hand-spinning of this sort becomes a basic cottage industry throughout the world.
The spinner uses one hand to draw out the fibres from the bundle of wool, cotton or flax, thus extending the half-spun thread to which the spindle is attached. The other hand gives a rotating flick to the spindle whenever it begins to lose impetus. Hand-spinning of this sort becomes a basic cottage industry throughout the world.
Loom: from 6000 BC
Weaving of cloth requires a loom - a structure which will hold taut the vertical threads (the warp), while the weaver snakes each horizontal thread in and out to form the weft. When the threads of the weft are pressed down tight, to form a solid mesh with the warp, a section of the cloth at the bottom of the loom is complete. A pattern is achieved by varying the colour of the threads in warp and weft.
The earliest known evidence of a loom comes from Egypt in about 4400 BC, but some method of supporting the warp exists from the beginning of weaving. The threads must either be suspended (and held taut by a weight at the bottom) or else must be stretched in the rigid frame of a conventional loom.
The earliest known evidence of a loom comes from Egypt in about 4400 BC, but some method of supporting the warp exists from the beginning of weaving. The threads must either be suspended (and held taut by a weight at the bottom) or else must be stretched in the rigid frame of a conventional loom.
Weaving: from 6000 BC
Until recently the earliest known scraps of cloth are woven from wool; dating from about 5800 BC, they come from Catal Huyuk in Anatolia. Similarly the first known example of linen has been from about 5000 BC in Egypt, where flax (an indigenous wild plant in the Mediterranean region) is cultivated. But a small woven fragment discovered in 1993 near the upper reaches of the Tigris probably pushes back the available evidence. It appears to be linen and has been dated to about 7000 BC.
Cotton is grown in both Eurasia and America; woven cotton survives from about 2500 BC in the Indus valley and slightly later in Peru. The most precisely localized source of any major fabric is China, where pieces of woven Silk are known from about 2850 BC.
Cotton is grown in both Eurasia and America; woven cotton survives from about 2500 BC in the Indus valley and slightly later in Peru. The most precisely localized source of any major fabric is China, where pieces of woven Silk are known from about 2850 BC.
The first miners: from 4000 BC
By 4000 BC deep shafts are cut into the hillside at Rudna Glava, in the Balkans, to excavate copper ore. This robbing of the earth's treasures is carried out with due solemnity. Fine pots, bearing produce from the daylight world, are placed in the mines as a form of recompense to propitiate the spirits of the dark interior of the earth.
By about 3800 BC copper mines are also worked in the Sinai peninsula. Crucibles found at the site reveal that smelting is carried out as part of the mining process.
By about 3800 BC copper mines are also worked in the Sinai peninsula. Crucibles found at the site reveal that smelting is carried out as part of the mining process.
Yoke and harness: from 4000 BC
The harnessing of draught animals is a major technological advance in agriculture as well as transport. The first to be harnessed is the ox, conveniently provided by nature with a fleshy hump above the shoulders. A yoke laid in front of this will remain in place even when a heavy burden is pulled. Sometimes a lighter yoke is attached to the horns. Oxen are dragging heavy objects or loaded Sledges by about 4000 BC.
The camel has an even more convenient hump. Its height makes it less suitable for draught purposes than the ox, but from perhaps 1000 BC it is used in Asia and north Africa for drawing wagons and for ploughing. By contrast, harnessing the horse proves problematical.
The camel has an even more convenient hump. Its height makes it less suitable for draught purposes than the ox, but from perhaps 1000 BC it is used in Asia and north Africa for drawing wagons and for ploughing. By contrast, harnessing the horse proves problematical.
A traditional yoke can only be kept in place on a horse by passing thongs in front of its chest. However carefully they are placed, these must pass in front of the animal's windpipe. The heavier the weight it attempts to pull, the less air it will breathe.
For many centuries this means that horses are not very effectively used as draught animals. The solution, discovered in China by the 5th century AD, is to provide a firm collar, fitting round the neck and shoulders of the animal to distribute the weight. Collars of this kind reach Europe by the 9th century AD, enabling the horse to become the main draught animal of the region for both ploughing and haulage.
For many centuries this means that horses are not very effectively used as draught animals. The solution, discovered in China by the 5th century AD, is to provide a firm collar, fitting round the neck and shoulders of the animal to distribute the weight. Collars of this kind reach Europe by the 9th century AD, enabling the horse to become the main draught animal of the region for both ploughing and haulage.
The plough and draught animals: from 3000 BC
The plough is almost certainly the first implement for which humans use a source of power other than their own muscles.
When planting seeds, it is essential to break up the ground. In the early stages of agriculture this is achieved by hacking and scraping with a suitably pointed implement - the antler of a deer, or a hooked branch of a tree. But a useful furrow can more easily be achieved by dragging a point along the surface of the ground. The first ploughs consist of a sharp point of timber, sometimes hardened in a flame or tipped with flint, projecting downwards at the end of a long handle.
When planting seeds, it is essential to break up the ground. In the early stages of agriculture this is achieved by hacking and scraping with a suitably pointed implement - the antler of a deer, or a hooked branch of a tree. But a useful furrow can more easily be achieved by dragging a point along the surface of the ground. The first ploughs consist of a sharp point of timber, sometimes hardened in a flame or tipped with flint, projecting downwards at the end of a long handle.
In the light soil of Egypt and Mesopotamia, where ploughing is first undertaken, a simple pointed implement of this kind is sufficient to break up the earth and form a shallow trench. Such a plough can be dragged by a couple of men. But the use of draught animals such as oxen, from at least 3000 BC, greatly speeds up the process.
In northern Europe, with heavier soil, this type of plough is ineffective. A more elaborate machine is developed, probably by the Celts in the 1st century BC, in which a sharb blade cuts into the earth and an angled board turns it over to form a furrow.
In northern Europe, with heavier soil, this type of plough is ineffective. A more elaborate machine is developed, probably by the Celts in the 1st century BC, in which a sharb blade cuts into the earth and an angled board turns it over to form a furrow.
The potter's wheel: 3000 BC
When a pot is built up from the base by hand, it is impossible that it should be perfectly round. The solution to this problem ia the potter's wheel, which has been a crucial factor in the history of ceramics. It is not known when or where the potter's wheel is introduced. Indeed it is likely that it develops very gradually, from a platform on which the potter turns the pot before shaping another side (thus avoiding having to walk around it).
By about 3000 BC a simple revolving wheel is a part of the potter's equipment in Mesopotamia, the cradle of so many innovations.
By about 3000 BC a simple revolving wheel is a part of the potter's equipment in Mesopotamia, the cradle of so many innovations.
The wheel: 3000 BC
The wheel is often quoted as the single most important advance in early technology. It is sometimes said to have evolved from the potter's wheel. Both are first known at approximately the same period, around 3000 BC. But they share no geographical origin and it is intrinsically unlikely that either form would suggest the other. Each is a natural solution to a very different problem.
In early technology a Wagon wheel can only be made from wood. Several of the earliest known wheels have been found in the heavily forested regions of Europe.
In early technology a Wagon wheel can only be made from wood. Several of the earliest known wheels have been found in the heavily forested regions of Europe.
Greece and Rome
Mechanical gearing: from 350 BC
An important adaptation of the wheel in technology is the pulley - a wheel round which a rope is run to exert force on an object at the other end. Such a machine is first mentioned in a Greek text of the 4th century BC, but it is likely to have been known much earlier.
In the simplest pulley a single wheel is used (as in hauling a flag up a flagpole). But major mechanical advantages can be achieved with two or more wheels - making it possible to lift a heavier object, albeit more slowly. The effect of two pulleys is that a force capable of pulling the rope two yards at one end will exert twice that force over a distance of only one yard at the other. The effect increases dramatically the more pulleys there are.
In the simplest pulley a single wheel is used (as in hauling a flag up a flagpole). But major mechanical advantages can be achieved with two or more wheels - making it possible to lift a heavier object, albeit more slowly. The effect of two pulleys is that a force capable of pulling the rope two yards at one end will exert twice that force over a distance of only one yard at the other. The effect increases dramatically the more pulleys there are.
A closely related mechanical principle for lifting is the lever, where a non-central fulcrum means that a weak force exerted at one end of a rigid bar becomes a stronger force over a shorter distance at the other end. This discovery is often linked with Greek science, because of the legendary remark attributed to Archimedes in the 3rd century BC: 'Give me a fulcrum and I will move the earth.'
In fact the lever has much earlier origins. It is probably the first mechanical device used in technology. From about 3000 BC the principle is put to practical use in both Egypt and Mesopotamia.
In fact the lever has much earlier origins. It is probably the first mechanical device used in technology. From about 3000 BC the principle is put to practical use in both Egypt and Mesopotamia.
Another important mechanical principle, that of The screw, is also commonly associated with Archimedes. The concept may have been discovered much earlier in Egypt, or by Greeks before the time of Archimedes. But as a system of raising water, The screw has long been linked with his name.
A different application, The screw press, is developed in Mediterranean regions at some time before the 1st century AD. Considerable pressure is needed to extract oil from olives. In earlier presses this is achieved by a heavy beam, on a lever principle. But a screw is more relentlessly effective, increasing the pressure to a new level with each turn.
A different application, The screw press, is developed in Mediterranean regions at some time before the 1st century AD. Considerable pressure is needed to extract oil from olives. In earlier presses this is achieved by a heavy beam, on a lever principle. But a screw is more relentlessly effective, increasing the pressure to a new level with each turn.
Rotary power: c.200 BC
The turning of a drum by pressure on projecting arms (the principle of the capstan or windlass) is a necessary part of any rotary machine, such as a screw press. The same principle makes it possible to grind corn between millstones.
The manual grinding of grain, together with the baking of bread, go back at least 8000 years to settled communities such as Catal Huyuk. Early forms of grinding involve rubbing one hard surface against another by hand (the pestle and mortar is one such method). Rotary mills, turned by slaves or animals, are known from at least the 2nd century BC.
The manual grinding of grain, together with the baking of bread, go back at least 8000 years to settled communities such as Catal Huyuk. Early forms of grinding involve rubbing one hard surface against another by hand (the pestle and mortar is one such method). Rotary mills, turned by slaves or animals, are known from at least the 2nd century BC.
Millstones: 2nd century BC
The milling of grain into flour, previously done by hand on a rough flat stone, achieves a major technological advance with the introduction of heavy stones which grind against each other to crush the seeds between them. The first mention of such stones is by a Roman author of the 2nd century BC, and many have been found at Pompeii.
The bottom stone is flat and circular, like a cheese, but the top one is tall and waisted - with a hole through it for grain to trickle down to the grinding surface. The upper stone is turned by pressure against wooden posts set into its waisted centre. Mills of this kind, when driven by asses or horses, are the first industrial use of animal power.
The bottom stone is flat and circular, like a cheese, but the top one is tall and waisted - with a hole through it for grain to trickle down to the grinding surface. The upper stone is turned by pressure against wooden posts set into its waisted centre. Mills of this kind, when driven by asses or horses, are the first industrial use of animal power.
Water mills: 1st century BC
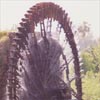
The emergence of the water mill is too gradual to be pinpointed. It is perhaps a development of a different form of water wheel. Once Rotary power is available, a simple gear will transfer it to the shaft or axle of a wheel. And a vertical wheel, with jugs attached to its rim, will perform the useful function of raising water by scooping it up at the bottom and pouring it out at the top.
Such water wheels, worked by oxen or camels, are in use in many parts of the world even today. They may well have been the distant inspiration of the water mill, where the process is reversed - the wheel itself being turned by water, and the power transferred in the other direction along the axle.
Such water wheels, worked by oxen or camels, are in use in many parts of the world even today. They may well have been the distant inspiration of the water mill, where the process is reversed - the wheel itself being turned by water, and the power transferred in the other direction along the axle.
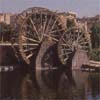
In an even simpler version of a water mill, a horizontal water wheel in a stream can turn a millstone above by means of a fixed shaft. Water mills of one kind or the other are certainly known by the 1st century BC in the Hellenistic world. A poem of the time advises young girls that they can now let the nymphs of the stream do the hard work of Milling.
The Romans adopt the Greek water mill, and Vitruvius in the 1st century BC gives the first written account of a geared water wheel. But the Romans do not apply the principle widely. The widespread and effective use of water power will be a technological achievement of the Middle Ages.
The Romans adopt the Greek water mill, and Vitruvius in the 1st century BC gives the first written account of a geared water wheel. But the Romans do not apply the principle widely. The widespread and effective use of water power will be a technological achievement of the Middle Ages.
Cement: c.200 BC
Builders in Greek cities on the coast of Turkey (and in particular Pergamum) evolve cement in about 200 BC as a structural material, in place of weaker mortars such as gypsum plaster (used in Egypt) or bitumen (in Mesopotamia). The secret of the new material is the lime which binds sand, water and clay.
The Romans subsequently use finely ground volcanic lava in place of clay, deriving it mainly from the region of Pozzuoli. Their cement, known for this reason as pozzolanic, is the strongest mortar in history until the development of Portland cement. When small fragments of volcanic rubble are included, the result is concrete - making possible the great arches and aqueducts of Roman architecture, and playing its part in Roman roads.
The Romans subsequently use finely ground volcanic lava in place of clay, deriving it mainly from the region of Pozzuoli. Their cement, known for this reason as pozzolanic, is the strongest mortar in history until the development of Portland cement. When small fragments of volcanic rubble are included, the result is concrete - making possible the great arches and aqueducts of Roman architecture, and playing its part in Roman roads.
Roman roads: 2nd century BC - 2nd century AD
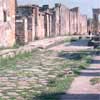
The great network of Roman roads, the arterial system of the empire, is constructed largely by the soldiers of the legions, often with the assistance of prisoners of war or slave labour. The amount of labour involved is vast, for these highways are elaborate technological undertakings.
The average width of a Roman road is about 10 yards. Below the paved surface the fabric extends to a depth of 4 or 5 feet in a succession of carefully constructed layers.
The average width of a Roman road is about 10 yards. Below the paved surface the fabric extends to a depth of 4 or 5 feet in a succession of carefully constructed layers.
First a trench is excavated. Its bottom is rammed hard, and if necessary is strengthened by driving in piles. Then four successive layers are constructed, each a foot or more thick. The first is of masonry, laid in cement or clay. Above this is a course of concrete, then gravel and cement. Finally the top layer is laid in dressed stones, sloping away in a pronounced camber from the centre.
The designers of the Roman roads are single-minded. Paying scant attention to the demands of contours, and having few property rights to consider, their mission is to drive the road straight ahead. The legions will march far in the empire, but they will take the shortest route.
The designers of the Roman roads are single-minded. Paying scant attention to the demands of contours, and having few property rights to consider, their mission is to drive the road straight ahead. The legions will march far in the empire, but they will take the shortest route.
Part of the purpose of the Roman roads is speed of communication, so there are posthouses with fresh horses every 10 miles along the route and lodgings for travellers every 25 miles. By the 2nd century AD the network spreads all round the Mediterranean and throughout Europe up to the Danube, the Rhine and northern England, amounting in all to some 50,000 miles. This far outdoes even the very impressive achievement of the Persian roads . Travellers on foot or horseback have rarely been so well provided for.
For haulage purposes these roads are less satisfactory, because the straight line results in some very steep hills. Anyone with a wagon and horse would prefer an attitude less severe than that of the Roman road engineer.
For haulage purposes these roads are less satisfactory, because the straight line results in some very steep hills. Anyone with a wagon and horse would prefer an attitude less severe than that of the Roman road engineer.
Arch vault and dome: from the 1st century BC
The greatest achievement of Roman architecture and technology lies in the development of these three architectural forms. The dome has long been a familiar concept (appearing dramatically in the passage grave on the Île Longue or in the tholos at Mycenae), but nothing has been made of it in the major architectural traditions. The spectacular temples of Egypt or Greece are exclusively trabeate, using flat horizontal lintels to span open spaces.
The arch has far greater capabilities than the lintel, for it can combine many smaller units (of stone or brick) to make a greater whole. In Greek architecture a single vast stone lintel can reach between columns at most 7 yards apart. A Roman brick arch can span 50 yards.
The arch has far greater capabilities than the lintel, for it can combine many smaller units (of stone or brick) to make a greater whole. In Greek architecture a single vast stone lintel can reach between columns at most 7 yards apart. A Roman brick arch can span 50 yards.
The arch, the vault and the dome are all applications of the same concept. The vault, or open-ended tunnel, is only an exceptionally deep arch. The dome is in effect a collection of arches all sharing the same centre. In each case the pressure of gravity on the material forming the arch will hold it together as long as the outward thrust is contained by buttresses.
The Roman achievement in all these forms is greatly assisted by their development of Concrete. An arch or dome bonded into solid form by a strong inner layer of Concrete sits as one unit, exerting its weight downwards rather than outwards. This makes possible such miracles as the 1st-century Pont du Gard or the 2nd-century dome of the Pantheon.
The Roman achievement in all these forms is greatly assisted by their development of Concrete. An arch or dome bonded into solid form by a strong inner layer of Concrete sits as one unit, exerting its weight downwards rather than outwards. This makes possible such miracles as the 1st-century Pont du Gard or the 2nd-century dome of the Pantheon.
The Pont du Gard: AD c.20
The scale of Roman architectural ambition is superbly seen in the great aqueduct at Nîmes, known as the Pont du Gard ('bridge of the Gard'). Constructed in about AD 20, this gigantic structure is purely practical. It is a section of a channel bringing water from the river Eure to the new Roman town of Nîmes.
The water flows gently downhill for a distance of almost 50 km. The Pont du Gard, with its three towering tiers of arches, carries it over the deep valley of the river Gard - in itself a source of water nearer to Nîmes, but too low-lying to reach the town by gravity.
The water flows gently downhill for a distance of almost 50 km. The Pont du Gard, with its three towering tiers of arches, carries it over the deep valley of the river Gard - in itself a source of water nearer to Nîmes, but too low-lying to reach the town by gravity.
Roman bridges: 1st - 2nd century AD
Bridges are as much part of the Roman architectural achievement as Aqueducts, and they present even greater constructional problems.
Some of the most impressive Roman bridges are over ravines. A fine surviving example, built for Trajan in AD 105, spans the Tagus in Spain, at Alcántara. Its two massive central arches, 110 feet wide and 210 feet above the normal level of the river, are made of uncemented granite. Each wedge-shaped block weighs 8 tons. During construction these blocks are winched into place by a system of pulleys, powered perhaps by slave labour on a treadmill. They are supported on a huge timber structure standing on the rocks below - to be removed when the arch is complete.
Some of the most impressive Roman bridges are over ravines. A fine surviving example, built for Trajan in AD 105, spans the Tagus in Spain, at Alcántara. Its two massive central arches, 110 feet wide and 210 feet above the normal level of the river, are made of uncemented granite. Each wedge-shaped block weighs 8 tons. During construction these blocks are winched into place by a system of pulleys, powered perhaps by slave labour on a treadmill. They are supported on a huge timber structure standing on the rocks below - to be removed when the arch is complete.
An equally remarkable feat of Roman construction is the building of bridges across rivers where no rock or island emerges from the water to carry the piers. An example survives in Rome - the Sant'Angelo bridge, built for Hadrian in AD 134 as an approach to his great circular mausoleum, now the Castel Sant'Angelo.
The building of such bridges is made possible by the Roman perfection of cement and Concrete, and by their invention of the Cofferdam.
The building of such bridges is made possible by the Roman perfection of cement and Concrete, and by their invention of the Cofferdam.
Roman cofferdams: 2nd century AD
A cofferdam is a watertight sheath within which the foundation of a bridge can be constructed in the bed of a river. The Roman pioneers of this technology drive two circles of wooden piles into the river and then pack the space between them with clay to achieve the watertight seal. The water and the mud of the river bed are scooped out of the resulting cylinder so that a concrete foundation for the pier can be constructed on firm ground.
The arches of the Sant'Angelo bridge still stand on foundations created in the Tiber in this way nearly 1900 years ago.
The arches of the Sant'Angelo bridge still stand on foundations created in the Tiber in this way nearly 1900 years ago.
Hero's dioptra: 1st century AD
One of the surviving books of Hero of Alexandria, entitled On the Dioptra, describes a sophisticated technique which he has developed for the surveying of land. Plotting the relative position of features in a landscape, essential for any accurate map, is a more complex task than simply measuring distances.
It is necessary to discover accurate angles in both the horizontal and vertical planes. To make this possible a surveying instrument must somehow maintain both planes consistently in different places, so as to take readings of the deviation in each plane between one location and another.
It is necessary to discover accurate angles in both the horizontal and vertical planes. To make this possible a surveying instrument must somehow maintain both planes consistently in different places, so as to take readings of the deviation in each plane between one location and another.
This is what Hero achieves with the instrument mentioned in his title, the dioptra - meaning, approximately, the 'spyhole' through which the surveyor looks when pinpointing the target in order to read the angles.
Hero adapts, for this new and dificult task, an instrument long used by Greek astronomers (such as Hipparchus) for measuring the angle of stars in the sky. It is evident from his description that the dioptra differs from the modern theodolite in only two important respects. It lacks the added convenience of two inventions not available to Hero - the Compass and the Telescope.
Hero adapts, for this new and dificult task, an instrument long used by Greek astronomers (such as Hipparchus) for measuring the angle of stars in the sky. It is evident from his description that the dioptra differs from the modern theodolite in only two important respects. It lacks the added convenience of two inventions not available to Hero - the Compass and the Telescope.
Knitting: from the 3rd century AD
Knitting, as a concept, is very simple but extremely hard to imagine. It is likely, therefore, to be one of the few technological developments in ancient history to have an actual inventor. As a challenge to the inventive mind, the problem ('Transform a continuous thread into a piece of fabric without at any point cutting the thread') still seems difficult.
The likelihood of a single moment of invention is also made more probable by the late arrival of knitting. Even though it makes no technological demands (neolithic communities could provide a skein of wool and two long needles), civlization is 3000 years old before the first row is knitted.
The likelihood of a single moment of invention is also made more probable by the late arrival of knitting. Even though it makes no technological demands (neolithic communities could provide a skein of wool and two long needles), civlization is 3000 years old before the first row is knitted.
Knitting first appears in the Roman empire, in the 3rd century AD. The earliest examples to survive are socks (found in tombs in Egypt), and it is in footwear that the advantages of the new technology are most obvious.
Until this time feet have usually been kept warm and protected within the shoe by wrapping them in strips of cloth or leather. In the 2nd century AD the Romans evolve a tailored sock, made of pieces of cloth sewn together. But these lack the elasticity of a knitted fabric. Eventually the demand for knitted stockings is so great that the first Knitting machine, devised in 1589, is an early landmark of the Industrial Revolution.
Until this time feet have usually been kept warm and protected within the shoe by wrapping them in strips of cloth or leather. In the 2nd century AD the Romans evolve a tailored sock, made of pieces of cloth sewn together. But these lack the elasticity of a knitted fabric. Eventually the demand for knitted stockings is so great that the first Knitting machine, devised in 1589, is an early landmark of the Industrial Revolution.
Middle Ages
Medieval technology: 7th - 14th century AD
Though there is bold innovation in medieval architecture, Europe in the Middle Ages is not notable for technological ingenuity in many other fields.
The Windmill is a medieval achievement. So is Clockwork, and Tidal power. But more immediately effective, in practical terms, is the widespread application of a source of power already used in Greek and roman times - that of the water mill. By the 14th century water mills are familiar in most parts of Europe with fast-flowing streams. And they are not limited to rotary purposes, such as turning millstones to grind corn. Mills now power great hammers which crush ore extracted from copper and silver mines, or which Full cloth in the textile industry.
The Windmill is a medieval achievement. So is Clockwork, and Tidal power. But more immediately effective, in practical terms, is the widespread application of a source of power already used in Greek and roman times - that of the water mill. By the 14th century water mills are familiar in most parts of Europe with fast-flowing streams. And they are not limited to rotary purposes, such as turning millstones to grind corn. Mills now power great hammers which crush ore extracted from copper and silver mines, or which Full cloth in the textile industry.
Windmills: 9th - 15th century AD
The first practical windmills are constructed in or before the 9th century in a region spanning eastern Iran and western Afghanistan. They are descibed in a manuscript by Estakhri, a Persian georgrapher of that period, as having horizontal sails, like the blades of a helicopter, directly linked by a vertical shaft to the millstones turning below. The date of the first windmill is often given as 644 or earlier, because a 9th-century document says that the man who in that year assassinated the caliph Omar in the mosque at Medina was a Persian builder of windmills. But a first mention of this two centuries after the event makes it unlikely to be true.
Windmills are first mentioned in Europe in the 12th century. There is a reference to one in France in 1180, and a few years later to another in England. Since this is the time of the crusades, it is likely that the idea has been brought from the Middle East.
Windmills are first mentioned in Europe in the 12th century. There is a reference to one in France in 1180, and a few years later to another in England. Since this is the time of the crusades, it is likely that the idea has been brought from the Middle East.
The European windmills of the 12th and 13th century have upright sails, of the kind still familiar today. They require simple gearing, to transmit the power to the vertical shaft which will turn the millstones. And they have to be able to turn through 360 degrees so that the sails can face the wind.
In these first versions the entire working mill, complete with the millstones, has to be turned into the wind by pressure from ground level on a long pole. For this to be possible the mill structure has to sit on a sturdy vertical post, giving such mills their name - post mills.
In these first versions the entire working mill, complete with the millstones, has to be turned into the wind by pressure from ground level on a long pole. For this to be possible the mill structure has to sit on a sturdy vertical post, giving such mills their name - post mills.
By the 14th century there are windmills of a new design in France. Known as tower mills, they can be larger and more rigid than the earlier post mills. Now only the top part of the structure rotates. Holding the horizontal axle of the sails, it sits like a loose cap on top of the mill tower. It can be turned either by the traditional pole, from outside, or by a lever within the cap.
By the 15th century windmills are common in Europe, though rarely as economical as the watermill. The exception is the Netherlands, where there is plenty of wind and a great deal of surplus water to be lifted from low-lying areas - the original purpose of the Dutch windmills.
By the 15th century windmills are common in Europe, though rarely as economical as the watermill. The exception is the Netherlands, where there is plenty of wind and a great deal of surplus water to be lifted from low-lying areas - the original purpose of the Dutch windmills.
Flash locks and pound locks: 10th - 15th century AD
From the very first construction of canals, some method is necessary to cope with differences in water level. The simplest solution is a weir, to hold up the water on the higher side, with a gap in the middle which can be opened to let a boat through. The removal of the barrier, however achieved, is inevitably followed by a sudden rush of water - carrying the vessel easily through in one direction, but making passage very difficult in the other. A primitive lock of this kind is known, for obvious reasons, as a flash lock.
The development of the more sophisiticated pound lock is traditionally credited to an engineer, Chiao Wei-yo, working on the great Chinese canal system in the 10th century AD.
The development of the more sophisiticated pound lock is traditionally credited to an engineer, Chiao Wei-yo, working on the great Chinese canal system in the 10th century AD.
It is said that Chiao is required to construct two flash locks on the Grand canal only about 200 yards apart. He realizes that he has created a pool which will be at the upper or lower level of the canal depending on which of the two barriers is open. Moreover the barrier separating patches of level water can be opened without the obstruction of water pressure.
The result is the pound lock, standard on all modern canals. The first in Europe is believed to have been built in the Netherlands in 1373 at Vreeswijk, where a canal from Utrecht joins the river Lek.
The result is the pound lock, standard on all modern canals. The first in Europe is believed to have been built in the Netherlands in 1373 at Vreeswijk, where a canal from Utrecht joins the river Lek.
At this stage the barrier is a simple sluicegate which has to be raised and lowered like a guillotine. The process is laborious, and the water pressure against the flat surface requires a very strong construction to hold it.
The last missing piece in the design of the modern lock is the mitred lock gate. On this system each end of the lock is closed by a pair of wooden gates slightly too large to close in a normal flush position. They meet with mitred edges pointing in the direction of the higher water level. Water pressure holds them tightly together, until the level is the same on either side - at which point the gates can be easily pushed open.
The last missing piece in the design of the modern lock is the mitred lock gate. On this system each end of the lock is closed by a pair of wooden gates slightly too large to close in a normal flush position. They meet with mitred edges pointing in the direction of the higher water level. Water pressure holds them tightly together, until the level is the same on either side - at which point the gates can be easily pushed open.
The first lock with mitred gates is probably the one built in Milan in about 1500 to join two Canals of differing levels. Known as the San Marco lock, it is likely that its design is by Leonardo da Vinci. As his notebooks reveal, Leonardo is interested in all aspects of hydraulic engineering; and he is employed at this time by the duke of Milan.
From the 12th century Europeans have been busy constructing Canals, even with the primitive device of the flash lock. The mitre lock makes possible increasingly ambitious projects.
From the 12th century Europeans have been busy constructing Canals, even with the primitive device of the flash lock. The mitre lock makes possible increasingly ambitious projects.
Tidal power: 11th - 12th century AD
Tide mills, damming a tidal stream at high tide to power a water wheel once the tide has fallen, are pioneered in England. Such a mill, built near the entrance to the port of Dover in about 1070, features in the records because it proves a danger to shipping. But tidal mills working without obstruction are mentioned at Bromley-le-Bow near London in 1135 and at Woodbridge in Suffolk in 1170.
In subsequent centuries many tidal mills are built on the coasts of Britain and on the Atlantic coasts of Europe and colonial America. They remain commercially effective for just as long as their more conventional inland cousins, powered by tumbling streams.
In subsequent centuries many tidal mills are built on the coasts of Britain and on the Atlantic coasts of Europe and colonial America. They remain commercially effective for just as long as their more conventional inland cousins, powered by tumbling streams.
A tower clock in China: AD 1094
After six years' work, a Buddhist monk by the name of Su Song completes a great tower, some thirty feet high, which is designed to reveal the movement of the stars and the hours of the day. Figures pop out of doors and strike bells to signify the hours.
The power comes from a water wheel occupying the lower part of the tower. Su Song has designed a device which stops the water wheel except for a brief spell, once every quarter of an hour, when the weight of the water (accumulated in vessels on the rim) is sufficient to trip a mechanism. The wheel, lurching forward, drives the machinery of the tower to the next stationary point in a continuing cycle.
The power comes from a water wheel occupying the lower part of the tower. Su Song has designed a device which stops the water wheel except for a brief spell, once every quarter of an hour, when the weight of the water (accumulated in vessels on the rim) is sufficient to trip a mechanism. The wheel, lurching forward, drives the machinery of the tower to the next stationary point in a continuing cycle.
This device (which in Su Sung's tower must feel like a minor earthquake every time it slams the machinery into action) is an early example of an escapement - a concept essential to mechanical Clockwork. In any form of clock based on machinery, power must be delivered to the mechanism in intermittent bursts which can be precisely regulated. The rationing of power is the function of the escapement. The real birth of mechanical Clockwork awaits a reliable version, developed in Europe in the 13th century.
Meanwhile Su Sung's tower clock, ready for inspection by the emperor in 1094, is destroyed shortly afterwards by marauding Barbarians from the north.
Meanwhile Su Sung's tower clock, ready for inspection by the emperor in 1094, is destroyed shortly afterwards by marauding Barbarians from the north.
Clockwork in Europe: 13th - 14th century AD
Europe at the end of the Middle Ages is busy trying to capture time. The underlying aim is as much astronomical (to reflect the movement of the heavenly bodies) as it is to do with the more mundane task of measuring everybody's day. But the attraction of that achievement is recognized too. A textbook on astronomy, written by 'Robert the Englishman' in 1271, says that 'clockmakers are trying to make a wheel which will make one complete revolution' in each day, but that 'they cannot quite perfect their work'.
What prevents them even beginning to perfect their work is the lack of an escapement. But a practical version of this dates from only a few years later.
What prevents them even beginning to perfect their work is the lack of an escapement. But a practical version of this dates from only a few years later.
A working escapement is invented in about 1275. The process allows a toothed wheel to turn, one tooth at a time, by successive teeth catching against knobs projecting from an upright rod which oscillates back and forth. The speed of its oscillation is regulated by a horizontal bar (known as a foliot) attached to the top of the rod. The time taken in the foliot's swing can be regulated by moving weights in or out on each arm.
The function of the foliot is the same as that of the pendulum in modern clocks, but it is less efficient in that gravity is not helping it to oscillate. A very heavy weight is needed to power the clock, involving massive machinery and much friction.
The function of the foliot is the same as that of the pendulum in modern clocks, but it is less efficient in that gravity is not helping it to oscillate. A very heavy weight is needed to power the clock, involving massive machinery and much friction.
Nevertheless the foliot works to a degree acceptable at the time (a clock in the Middle Ages is counted a good timekeeper if it loses or gains only a quarter of an hour a day), and in the 14th century there are increasingly frequent references to clocks in European cities. A particularly elaborate one is built between 1348 and 1364 in Padua by Giovanni de' Dondi, a professor of astronomy at the university who writes a detailed description of his clock. A 14th-century manuscript of his text has the earliest illustration of a clock mechanism with its escapement.
The world's three oldest surviving examples of clockwork date from the last years of the 14th century.
The world's three oldest surviving examples of clockwork date from the last years of the 14th century.
The famous clock in Salisbury cathedral, installed by 1386 and still working today with its original mechanism, is a very plain piece of machinery. It has no face, being designed only to strike the hours. Striking is the main function of all early clocks (the word has links with the French cloche, meaning 'bell').
In 1389 a great clock is installed above a bridge spanning a street in Rouen. It remains one of the famous sights of the city, though its glorious gilded dial is a later addition and its Foliot has been replaced by a pendulum (in 1713). The historical distinction of the Rouen clock is that it is the first machine designed to strike the quarter-hours.
In 1389 a great clock is installed above a bridge spanning a street in Rouen. It remains one of the famous sights of the city, though its glorious gilded dial is a later addition and its Foliot has been replaced by a pendulum (in 1713). The historical distinction of the Rouen clock is that it is the first machine designed to strike the quarter-hours.
In 1392 the bishop of Wells instals a clock in his cathedral. The bishop has previously been in Salisbury, and the same engineer seems to have made the new clock. It not only strikes the quarters. It steals a march on Rouen by having a dial, showing the movement of astronomical bodies.
With escapements, chiming mechanisms and dials, clocks are now set to evolve into their more familiar selves. And the telling of time soon alters people's perceptions of time itself. Hours, minutes and seconds are units which only come into existence as the ability to measure them develops.
With escapements, chiming mechanisms and dials, clocks are now set to evolve into their more familiar selves. And the telling of time soon alters people's perceptions of time itself. Hours, minutes and seconds are units which only come into existence as the ability to measure them develops.
The first cloth mills: 13th century AD
The process of fulling cloth, in medieval Europe's important textile industry, is entirely manual until the 13th century. Woven cloth is fulled to give it extra strength by compressing and binding the fibres. Traditionally this has been done by prolonged pounding, by foot or hand, of cloth which is soaked in water and fuller's earth (to remove grease from the wool).
This heavy work is replaced in England, from the 13th century, by pounding with great wooden hammers. They are raised by tappets fixed to the shaft of a water wheel and are then released to fall by their own weight. It is the first step in the mechanization of textile production, which will eventually play such an important part in the Industrial revolution.
This heavy work is replaced in England, from the 13th century, by pounding with great wooden hammers. They are raised by tappets fixed to the shaft of a water wheel and are then released to fall by their own weight. It is the first step in the mechanization of textile production, which will eventually play such an important part in the Industrial revolution.
15th - 16th century
Gutenberg and western printing: AD 1439 - 1457
The name of Gutenberg first appears, in connection with printing, in a law case in Strasbourg in 1439. He is being sued by two of his business partners. Witnesses, asked about Gutenberg's stock, describe a press and a supply of metal type. It sounds as though he is already capable of printing small items of text from movable type, and it seems likely that he must have done so in Strasbourg. But nothing from this period survives.
By the time he is next heard of in connection with printing, he is in Mainz. He borrows 800 guilders in 1450 from Johann Fust with his printing equipment as security. The resulting story of Gutenberg and Fust is a saga in itself.
By the time he is next heard of in connection with printing, he is in Mainz. He borrows 800 guilders in 1450 from Johann Fust with his printing equipment as security. The resulting story of Gutenberg and Fust is a saga in itself.
Gutenberg's great achievement in the story of printing has several components. One is his development of the printing Press, capable of applying a rapid but steady downward pressure. The concept of the Press is not new. But existing presses (for wine, oil or paper) exert slow pressure - uneconomical in printing.
More significant are Gutenberg's skills with metal (his original trade is that of a goldsmith). These enable him to master the complex stages in the manufacture of individual pieces of Type, which involve creating a master copy of each letter, devising the moulds in which multiple versions can be cast, and developing a suitable alloy (Type metal) in which to cast them.
More significant are Gutenberg's skills with metal (his original trade is that of a goldsmith). These enable him to master the complex stages in the manufacture of individual pieces of Type, which involve creating a master copy of each letter, devising the moulds in which multiple versions can be cast, and developing a suitable alloy (Type metal) in which to cast them.
No date appears in the Gutenberg Bible (known technically as the 42-line Bible), which was printed simultaneously on six presses during the mid-1450s. But at least one copy is known to have been completed, with its initial letters coloured red by hand, by 24 August 1456. The first dated book from these same presses, in 1457, is even more impressive. Known as the Mainz psalter, it achieves outstanding colour printing in its two-colour initial letters.
These first two publications from Germany's presses are of an extraordinary standard, caused no doubt by the commercial need to compete with manuscripts. The new technology, so brilliantly launched, spreads rapidly.
These first two publications from Germany's presses are of an extraordinary standard, caused no doubt by the commercial need to compete with manuscripts. The new technology, so brilliantly launched, spreads rapidly.
All this skilful technology precedes the basic work of printing - that of arranging the individual letters, aligned and well spaced, in a forme which will hold them firm and level to transfer the ink evenly to the paper.
The printing process involves complex problems at every stage, and the brilliance of the first known products from Gutenberg's Press suggest that earlier efforts must have been lost. If not, the decision to make his first publication a full-length Bible in Latin (the Vulgate), printed to the standards of the best Black-letter manuscripts, is a bold one indeed.
The printing process involves complex problems at every stage, and the brilliance of the first known products from Gutenberg's Press suggest that earlier efforts must have been lost. If not, the decision to make his first publication a full-length Bible in Latin (the Vulgate), printed to the standards of the best Black-letter manuscripts, is a bold one indeed.
Domestic clocks: 15th century AD
After the success of the clocks in Europe's cathedrals in the late 14th century, and the introduction of the clock face in places such as Wells, kings and nobles naturally want this impressive technology at home.
The first domestic clocks, in the early 15th century, are miniature versions of the cathedral clocks - powered by hanging weights, regulated by escapements with a Foliot, and showing the time to the great man's family and household by means of a single hand working its way round a 12-hour circuit on the clock's face. But before the middle of the 15th century a development of great significance occurs, in the form of a spring-driven mechanism.
The first domestic clocks, in the early 15th century, are miniature versions of the cathedral clocks - powered by hanging weights, regulated by escapements with a Foliot, and showing the time to the great man's family and household by means of a single hand working its way round a 12-hour circuit on the clock's face. But before the middle of the 15th century a development of great significance occurs, in the form of a spring-driven mechanism.
The earliest surviving spring-driven clock, now in the Science Museum in London, dates from about 1450. By that time clockmakers have not only discovered how to transmit power to the mechanism from a coiled spring. They have also devised a simple but effective solution to the problem inherent in a coiled spring which steadily loses power as it uncoils.
The solution to this is the fusee.
The solution to this is the fusee.
The fusee is a cone, bearing a spiral of grooves on its surface, which forms part of the axle driving the wheels of the clock mechanism. The length of gut linking the drum of the spring to the axle is wound round the fusee. It lies on the thinnest part of the cone when the spring is fully wound and reaches its broadest circumference by the time the spring is weak. Increased leverage exactly counteracts decreasing strength.
These two devices, eliminating the need for weights, make possible clocks which stand on tables, clocks which can be taken from room to room, even clocks to accompany a traveller in a carriage. Eventually, most significant of all, they make possible the Pocket watch.
These two devices, eliminating the need for weights, make possible clocks which stand on tables, clocks which can be taken from room to room, even clocks to accompany a traveller in a carriage. Eventually, most significant of all, they make possible the Pocket watch.
17th - 18th century
Steam pump: AD 1698-1702
Thomas Savery has grown up in a mining district of Devon and knows the problem of flooded mines. In 1698 he obtains a patent for an engine to raise water 'by the Impellent Force of Fire'. It turns out to be the world's first practical steam engine. Designed purely as a pump, it has no piston but relies on the power of a vacuum.
A metal cylinder is filled with steam from a boiler. Cold water is poured over the outside, condensing the steam within and creating a vacuum which sucks water up through a pipe at the base. When the cylinder is full of water, the valve from below is closed. Steam is again introduced, forcing the water out of the cylinder through another valve. With the cylinder again full of steam, the process is repeated.
A metal cylinder is filled with steam from a boiler. Cold water is poured over the outside, condensing the steam within and creating a vacuum which sucks water up through a pipe at the base. When the cylinder is full of water, the valve from below is closed. Steam is again introduced, forcing the water out of the cylinder through another valve. With the cylinder again full of steam, the process is repeated.
In 1702 Savery publishes a book about his invention, entitled The Miner's Friend. In it he describes how the idea came to him. One evening, after finishing his wine, he threw the empty bottle into the fire and prepared to wash his hands in a basin of water. Noticing steam coming out of the neck of the bottle, he plucked it from the fire and stuck it neck down in the basin. As the bottle cooled, it sucked up the water.
The story sounds improbable, and it may be Savery's way of trying to justify his patent - for the principles involved are already well known to contemporary scientists. What the pamphlet does show is that Savery intends to make money from his invention by supplying pumps to mines.
The story sounds improbable, and it may be Savery's way of trying to justify his patent - for the principles involved are already well known to contemporary scientists. What the pamphlet does show is that Savery intends to make money from his invention by supplying pumps to mines.
As it turns out, the maximum levels of pressure and vacuum achieved by Savery cannot lift water more than about twelve yards - too little for most mines.
Instead he finds his main customers among progressive country landowners, who are attracted by being at the cutting edge of technology. They use Savery's pumps to raise water for their houses and gardens.
Instead he finds his main customers among progressive country landowners, who are attracted by being at the cutting edge of technology. They use Savery's pumps to raise water for their houses and gardens.
Boiler cylinder and piston: AD 1704-1712
Two Devon metalworkers - Thomas Newcomen, a Dartmouth blacksmith, and his assistant John Calley, a glassblower and plumber - are making good progress in some potentially very profitable experiments. They know the high cost of the horse-driven pumps which raise water from the copper and tin mines of Devon and Cornwall. So they are working on a steam pump.
Though probably unaware of this, they are combining two elements pioneered separately by Denis Papin and Thomas Savery - Papin's piston and Savery's separation of the boiler (providing the supply of steam) from the cylinder (where the steam does its work).
Though probably unaware of this, they are combining two elements pioneered separately by Denis Papin and Thomas Savery - Papin's piston and Savery's separation of the boiler (providing the supply of steam) from the cylinder (where the steam does its work).
In Newcomen's engine the piston, emerging from the top of the cylinder, is attached by an iron chain to one end of a beam which seesaws on a central pivot. At the other end of the beam another chain leads down to the water-pumping mechanism.
Steam released from the boiler into the cylinder pushes up the piston. When the cylinder is full of steam, the same procedure follows as in Savery's engine. Cold water poured on the outside condenses the steam and creates the vacuum. But in this case, instead of directly sucking up water, the vacuum causes the piston to descend in the cylinder. The chain drags down one end of the beam, activating the pump at the other end.
Steam released from the boiler into the cylinder pushes up the piston. When the cylinder is full of steam, the same procedure follows as in Savery's engine. Cold water poured on the outside condenses the steam and creates the vacuum. But in this case, instead of directly sucking up water, the vacuum causes the piston to descend in the cylinder. The chain drags down one end of the beam, activating the pump at the other end.
As so often in the advance of science and technology, an accident provides Newcomen with the refinement which brings his pump up to an economic speed. A flaw develops in one of the seams of his cylinder. As a result some cold water, intended only to flow down the outside, gets into the cylinder when it is full of steam. It creates a vacuum so rapid and so powerful that it snaps the chain attaching the piston to the beam.
With this event another lasting feature of the steam engine is discovered. In all Newcomen's developed engines, which soon start work in England's mines, the steam is condensed by a jet of cold water injected into the cylinder.
With this event another lasting feature of the steam engine is discovered. In all Newcomen's developed engines, which soon start work in England's mines, the steam is condensed by a jet of cold water injected into the cylinder.
The first of Newcomen's working engines is installed in 1712 at a colliery near Dudley Castle. It operates successfully here for some thirty years, as the first of many in the mining districts of Britain. Newcomen's machine undoubtedly infringes Savery's patent, for there is no denying that it works 'by the Impellent Force of Fire'. But Savery is having no great commercial success with his own machine. The two men come to an amicable arrangement, the details of which are not known.
Even with Newcomen's improvements, these machines are suitable only for the slow relentless work of pumping in the mines. Proof of the wider potential of the steam engine must await the inventive genius of James Savery.
Even with Newcomen's improvements, these machines are suitable only for the slow relentless work of pumping in the mines. Proof of the wider potential of the steam engine must await the inventive genius of James Savery.
A millennium clock: AD 1746
In 1746 a French clockmaker, Monsieur Passemont (his first name is not known), completes a clock which is almost certainly the first in the world to be able to take account of a new millennium. Its dials can reveal the date of the month in any year up to9999.
It is a Longcase clock, in an ornate baroque casing which conceals a mechanism consisting of more than 1000 interconnecting wheels and cogs. Their related movements, as they turn at their different speeds with each swing of the pendulum, are designed to cope with the complexities of the Julian calendar. Thus, for example, one large brass wheel has the responsibility of inserting February 29 in each leap year.
It is a Longcase clock, in an ornate baroque casing which conceals a mechanism consisting of more than 1000 interconnecting wheels and cogs. Their related movements, as they turn at their different speeds with each swing of the pendulum, are designed to cope with the complexities of the Julian calendar. Thus, for example, one large brass wheel has the responsibility of inserting February 29 in each leap year.
This particular wheel takes four years to complete a single revolution. When it has come full circle, it pops in the extra day. (M. Passemont decides, however, not to grapple with Gregorian refinements; the absence of February 29 in 1700, 1800 and 1900 has had to be manually achieved.)
Louis XV buys the clock in 1749, three years after its completion. It is still ticking away two and a half centuries later in the palace of Versailles. The minutiae of daily time-keeping are also adjusted by hand (the clock loses a minute a month), but Monsieur Passemont's masterpiece requires no assistance in making a significant change in the first digit of its year display - from 1 to 2, at midnight on 31 December 1999.
Louis XV buys the clock in 1749, three years after its completion. It is still ticking away two and a half centuries later in the palace of Versailles. The minutiae of daily time-keeping are also adjusted by hand (the clock loses a minute a month), but Monsieur Passemont's masterpiece requires no assistance in making a significant change in the first digit of its year display - from 1 to 2, at midnight on 31 December 1999.
This History is as yet incomplete.
Kay's flying shuttle: AD 1733
James Watt and the condenser: AD 1764-1769
In 1764 a model of a Newcomen steam engine is brought for repair to the young James Watt, who is responsible for looking after the instruments in the physics department of the university of Glasgow. In restoring it to working order, he is astonished at how much steam it uses and wastes.
The reason, he realizes, is that the machine's single cylinder is required to perform two opposing functions. It must receive the incoming steam at maximum pressure to force the piston up (for which it needs to be as hot as possible), and it must then condense the steam to form a vacuum to pull the cylinder down (for which it needs to be as cool as possible).
The reason, he realizes, is that the machine's single cylinder is required to perform two opposing functions. It must receive the incoming steam at maximum pressure to force the piston up (for which it needs to be as hot as possible), and it must then condense the steam to form a vacuum to pull the cylinder down (for which it needs to be as cool as possible).
The solution occurs to Watt when he is walking near Glasgow one Sunday in May 1765. The two functions could be separated by providing a chamber, outside the cylinder but connecting with it, in which a jet of cold water will condense the steam and cause the vacuum.
This chamber is the condenser, for which Watt registers a patent in 1769. The principle has remained an essential part of all subsequent steam engines. It is the first of three major improvements which Watt makes in the basic design of steam-driven machinery. The other two are the Double-acting engine and the Governor, developed in the 1780s.
This chamber is the condenser, for which Watt registers a patent in 1769. The principle has remained an essential part of all subsequent steam engines. It is the first of three major improvements which Watt makes in the basic design of steam-driven machinery. The other two are the Double-acting engine and the Governor, developed in the 1780s.
Early in the 1770s Watt goes into business with Matthew Boulton, an entrepreneur with a large factory at Soho near Birmingham. Boulton has the capacity to manufacture steam engines to Watt's patented design, and the first two are delivered to customers in 1776.
One of them, installed by Watt himself at John Wilkinson's ironworks at Broseley in Shropshire, is of special significance. Wilkinson is the only ironmaster in the country capable of producing cylinders of sufficiently accurate dimensions to deliver the potential benefits of Watt's improved engine.
One of them, installed by Watt himself at John Wilkinson's ironworks at Broseley in Shropshire, is of special significance. Wilkinson is the only ironmaster in the country capable of producing cylinders of sufficiently accurate dimensions to deliver the potential benefits of Watt's improved engine.
Hargreaves jenny and Cromptow's mule: AD 1764-1779
An accident is said to have given a Lancashire spinner, James Hargreaves, the idea for the first mechanical improvement of the spinning process. In about 1764 he notices an overturned spinning wheel which continues to turn with the spindle vertical rather than horizontal. This gives him the idea that several spindles could be worked simultaneously from a wheel in this position.
He develops a version with eight spindles for use by his own family, thus immediately raising their output eight times. News of this causes jealous local spinners to invade his house and smash his machines.
He develops a version with eight spindles for use by his own family, thus immediately raising their output eight times. News of this causes jealous local spinners to invade his house and smash his machines.
Hargreaves moves to Nottingham, where he sets up a small cotton-mill using his invention. It acquires the name of spinning jenny, traditionally explained as being the name of the daughter who gave Hargreaves the idea when she knocked over her spinning wheel. He patents his device in 1770. By the time of his death, in 1778, the latest versions of his machine work eighty spindles each - and there are said 20,000 jennies in use in the cottages and small factories of Britain.
This is still an entirely hand-operated mechanism. The next essential development is the application of power. This is solved by Richard Arkwright, who takes out a patent for his machine in 1769.
This is still an entirely hand-operated mechanism. The next essential development is the application of power. This is solved by Richard Arkwright, who takes out a patent for his machine in 1769.
Arkwright's innovation is in drawing out the cotton by means of rollers before it is twisted into yarn. He succeeds first with a machine worked by a horse, but two years later - in 1771 - he successfully applies water power, with the result that his invention becomes known as the water frame. It is in place just in time for an immense new expansion of the cotton industry after a high tax on pure-cotton fabrics (aimed at calicoes imported from India) is reduced in 1774.
Arkwright's machines are suitable for spinning the strong yarn required for the warp of the Woven cloth. They are less good at the finer material needed for the weft. Yet conversely, Hargreaves' spinning jenny is only suitable for the weft.
Arkwright's machines are suitable for spinning the strong yarn required for the warp of the Woven cloth. They are less good at the finer material needed for the weft. Yet conversely, Hargreaves' spinning jenny is only suitable for the weft.
The technologies of Arkwright and Hargreaves therefore complement each other for a few years until the merits of each are combined by Samuel Crompton, a worker in a Lancashire spinning mill. In doing so he takes the final step in the spinning technology of the early Industrial Revolution.
Crompton observes the tendency of the spinning jenny to break the yarn, and he resolves to improve this aspect of the process. He does so in a machine which he perfects in 1779.
Crompton observes the tendency of the spinning jenny to break the yarn, and he resolves to improve this aspect of the process. He does so in a machine which he perfects in 1779.
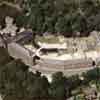
Crompton's machine combines the principles of Hargreaves' jenny and of Arkwright's water frame. The name which it acquires - Crompton's mule - is a pun on that fact. As the offspring of a jenny (a female donkey) and of another creature, the new arrival is clearly a mule.
Crompton's machine is capable of spinning almost every kind of yarn at considerable speed. The flying shuttle in the 1750s put pressure on the spinners to catch up. Now the mule challenges the weavers. They respond in 1785 with the first water-driven power loom, invented by Edmund Cartwright after visiting Arkwright's mills at Cromford. With all this technology in place, the pressure is now on the suppliers of raw Cotton in america.
Crompton's machine is capable of spinning almost every kind of yarn at considerable speed. The flying shuttle in the 1750s put pressure on the spinners to catch up. Now the mule challenges the weavers. They respond in 1785 with the first water-driven power loom, invented by Edmund Cartwright after visiting Arkwright's mills at Cromford. With all this technology in place, the pressure is now on the suppliers of raw Cotton in america.
Ironbridge: AD 1779
In the space of a few months in 1779 the world's first iron bridge, with a single span of over 100 feet, is erected for Abraham darby (the third of that name) over the Severn just downstream from Coalbrookdale. Work has gone on for some time in building the foundations and casting the huge curving ribs. But in this new technology little time need be spent in assembling the parts - which amount, it is proudly announced, to 378 tons 10 cwt. of metal.
The lightness of the structure strikes all observers. An early visitor comments: 'though it seems like network wrought in iron, it will be uninjured for ages.' It is uninjured still. A great tradition, bringing marvels such as the Crystal palace, begins in this industrial valley.
The lightness of the structure strikes all observers. An early visitor comments: 'though it seems like network wrought in iron, it will be uninjured for ages.' It is uninjured still. A great tradition, bringing marvels such as the Crystal palace, begins in this industrial valley.
This History is as yet incomplete.
Machine tools gun barrels and cylinders: AD 1774-1800
Double-acting engine and governor: AD 1782-1787
Just as James Watt applied a rational approach to improve the efficiency of the steam engine with the Condenser, so now he takes a logical step forward in a modification patented in 1782. His new improvement is the double-acting engine.
Watt observes that the steam is idle for half of each cycle. During the downward stroke, when the vacuum is exerting atmospheric force on the piston, the valve between boiler and cylinder is closed. Watt takes the simple step of diverting the steam during this part of the cycle to the upper part of the cylinder, where it joins with the atmospheric pressure in forcing the cylinder down - and thus doubles its effective action.
Watt observes that the steam is idle for half of each cycle. During the downward stroke, when the vacuum is exerting atmospheric force on the piston, the valve between boiler and cylinder is closed. Watt takes the simple step of diverting the steam during this part of the cycle to the upper part of the cylinder, where it joins with the atmospheric pressure in forcing the cylinder down - and thus doubles its effective action.
The most elegant contraption devised by Watt is in use from 1787. It is the governor - the first example of the type of controlling device required in industrial automation, and a feature of all steam engines since Watt's time.
Watt's governor consists of two arms, hinged on a central pivot and rotated by the action of the steam engine. Each arm has a heavy ball at the end. As the speed increases, centrifugal force moves the balls and the arms outwards. This action narrows the aperture of a valve controlling the flow of steam to the engine. As the power is slowly cut off, the speed of the engine reduces and the balls subside nearer to the central column - thus slightly opening the valve again in a permanent process of adjustment.
Watt's governor consists of two arms, hinged on a central pivot and rotated by the action of the steam engine. Each arm has a heavy ball at the end. As the speed increases, centrifugal force moves the balls and the arms outwards. This action narrows the aperture of a valve controlling the flow of steam to the engine. As the power is slowly cut off, the speed of the engine reduces and the balls subside nearer to the central column - thus slightly opening the valve again in a permanent process of adjustment.
Watt's many improvements to the steam engine leave it poised to undertake a whole new range of tasks. Its new efficiency means that it can become mobile. Each engine can now generate more power than is required merely to move itself.
By the time of his death in 1819, in quiet retirement near Birmingham, Watt has seen the introduction of commercially successful steam boats and the dawn of the railway age. In each case the vehicles are powered by engines of the type which he has developed.
By the time of his death in 1819, in quiet retirement near Birmingham, Watt has seen the introduction of commercially successful steam boats and the dawn of the railway age. In each case the vehicles are powered by engines of the type which he has developed.
This History is as yet incomplete.
Cotton gin: AD 1793
The mechanization of spinning and weaving in England, between 1733 and 1785, greatly speeds up the industrial process and rapidly leads to a shortage of cotton. During most of the century the bulk of raw cotton arriving at Liverpool for the Lancashire mills is from India. The cotton grown in the southern states of America is commercially less viable because it is short-fibred.
The cotton fibres, which will be spun into cotton, have to be separated from the seeds which they protect and enmesh. This process, known as cotton picking, is done entirely by hand. The short fibres make it a slow and expensive task.
The cotton fibres, which will be spun into cotton, have to be separated from the seeds which they protect and enmesh. This process, known as cotton picking, is done entirely by hand. The short fibres make it a slow and expensive task.
In 1793 Eli Whitney, a graduate of Yale, invents a machine which solves this problem. It consists of a hand-turned roller with projecting spikes. Each spike passes through a slot in a grid, wide enough to allow the spike to drag the cotton fibres through but too narrow for the cotton seeds to pass. They fall out into a separate container, while a revolving brush cleans the fibres, or lint, off the spikes.
Whitney's machine immediately trebles the speed at which cotton can be ginned, with major effects on the economy of the southern states of America. About forty times as much cotton (now established as 'king cotton') is produced in 1810 as in 1793. Vast new areas are taken in hand as plantations. The demand for slaves increases accordingly.
Whitney's machine immediately trebles the speed at which cotton can be ginned, with major effects on the economy of the southern states of America. About forty times as much cotton (now established as 'king cotton') is produced in 1810 as in 1793. Vast new areas are taken in hand as plantations. The demand for slaves increases accordingly.
19th century and beyond
Pont Cysyllte: AD 1795-1805
In 1795 Thomas Telford applies cast-iron technology in a bold new context. In 1793 he has been appointed engineer and architect to the Shropshire Union canal, which is to link the Mersey with the Severn. Near Llangollen the proposed route crosses the Dee valley, which is more than 300 yards wide and drops down about 120 feet to the river level below.
The number of locks needed to get a barge down and up again would represent a costly delay for the bargees. Yet an aqueduct of this height and length is a daunting project. The valley is much wider and deeper than the one spanned by Brindley in his heavily buttressed aqueduct at Barton. But Telford accepts the challenge.
The number of locks needed to get a barge down and up again would represent a costly delay for the bargees. Yet an aqueduct of this height and length is a daunting project. The valley is much wider and deeper than the one spanned by Brindley in his heavily buttressed aqueduct at Barton. But Telford accepts the challenge.
Telford constructs at Pont Cysyllte what is in effect an enormous cast-iron gutter. Cast to the correct curves and then welded together, Telford's plates combine to form a channel which is nearly 12 feet wide, with a path alongside for the carthorse. The metal is much lighter than the thick layer of pounded clay and sand used by Brindley to contain the water of the Bridgewater canal. So Telford's aqueduct can be a slender structure of nineteen tall stone arches.
Pont Cysyyllte is ready for the first barge to make the journey across the valley in 1805. Walter Scott describes it as 'the most impressive work of art' which he has ever seen.
Pont Cysyyllte is ready for the first barge to make the journey across the valley in 1805. Walter Scott describes it as 'the most impressive work of art' which he has ever seen.
The roads of Telford and McAdam: AD 1803-1815
Improvement in the speed of coaches, seen in Britain with the introduction of the Mail coach in 1784, is accompanied by similar advances in road technology. Travel in horse-drawn vehicles becomes increasingly sophisticated during a period of about fifty years, until the success of the railways results once again in roads being neglected. The early decades of the 19th century are the great days of coaching, commemorated in many paintings and prints.
Clear evidence of this new priority is the government's appointment of Thomas Telford in 1803 to undertake extensive public works in his native Scotland.
Clear evidence of this new priority is the government's appointment of Thomas Telford in 1803 to undertake extensive public works in his native Scotland.
Telford constructs more than 900 miles of road in Scotland, together with 120 bridges, before transferring his attention to the important route along the north coast of Wales (leading to Anglesey and the shipping lanes to Ireland). With justification Robert Southey describes Telford as the Colossus of Roads.
Meanwhile another Scot, John McAdam, has been making great improvements in the surface quality of the new roads. He devises a system, first put into practice in the Bristol region in 1815, for improving the durability of a carriage way.
Meanwhile another Scot, John McAdam, has been making great improvements in the surface quality of the new roads. He devises a system, first put into practice in the Bristol region in 1815, for improving the durability of a carriage way.
A McAdam road is well drained and is raised slightly above ground level. McAdam achieves this by laying three successive layers of graded stones, with the largest ones at the bottom. Each layer is compacted by a very simple method. The road is opened to traffic for several weeks, until the metal-rimmed wheels of carriages and carts have compressed and levelled the stones sufficiently for the next layer, of a finer grade, to be added.
Roads made by this method come to be known all over the world as macadamized. When tar is added to bind the top layer, later in the 19th century, the result is the tar macadam road - and eventually the trade name 'tarmac'.
Roads made by this method come to be known all over the world as macadamized. When tar is added to bind the top layer, later in the 19th century, the result is the tar macadam road - and eventually the trade name 'tarmac'.
Sections are as yet missing at this point.
Glass iron and prefabrication: AD 1837-1851
The public first becomes aware of the glorious potential of cast-iron architecture in the 1840s, when extraordinary conservatories are erected at Chatsworth and in Kew Gardens. But the technology derives from factory construction in the 1790s.
With Boulton and Watt's steam machinery in operation, conventional factories using timber for joists and floors are prone to disastrous fires. The occasional use of cast iron for structural purposes goes back many centuries in China, for temple pagodas, but it is an innovation in Britain when William Strutt builds the first fireproof mill at Derby, in 1792-3, with floors on shallow brick arches supported on cast-iron pillars.
With Boulton and Watt's steam machinery in operation, conventional factories using timber for joists and floors are prone to disastrous fires. The occasional use of cast iron for structural purposes goes back many centuries in China, for temple pagodas, but it is an innovation in Britain when William Strutt builds the first fireproof mill at Derby, in 1792-3, with floors on shallow brick arches supported on cast-iron pillars.
Strutt's mill still contains some massive wooden beams, but an entirely wood-free factory is constructed at Ditherington, near Shrewsbury, in 1796-7. Arched brick floors, on cast-iron beams and pillars, become the standard factory and warehouse interior of the 19th century.
The next and most glamorous stage in cast-iron architecture is linked above all with the name of Joseph Paxton. As superintendent of the duke of Devonshire's gardens at Chatsworth, he builds there in 1837-40 a great conservatory, shaped like a tent (277 feet long and 67 feet high) but consisting entirely of cast iron and glass.
The next and most glamorous stage in cast-iron architecture is linked above all with the name of Joseph Paxton. As superintendent of the duke of Devonshire's gardens at Chatsworth, he builds there in 1837-40 a great conservatory, shaped like a tent (277 feet long and 67 feet high) but consisting entirely of cast iron and glass.
In a ducal garden this building is not much visited, but it astonishes all who see it. Queen Victoria notes in her diary in 1842 that it is 'the most stupendous and extraordinary creation imaginable'. Two years later a similar building is commissioned from Richard Turner and Decimus Burton for the royal gardens at Kew. Since 1841 these gardens have been open to the public, so the beauty of the Palm House, completed in 1848, becomes more widely known than the Chatsworth conservatory.
But it is Paxton's building for the Great exhibition of 1851, the astonishing Crystal Palace, which reveals to the millions the potential of the new architecture.
But it is Paxton's building for the Great exhibition of 1851, the astonishing Crystal Palace, which reveals to the millions the potential of the new architecture.
The Crystal Palace is gigantic compared to its predecessors in cast iron and glass. It is five times as long as the Palm House in Kew and nearly twice as high; or, put another way, it is longer than the palace of Versailles and higher than Westminster Abbey. But even more significant is the famous speed of its design (one week of detailed drawing, after a preliminary jotting by Paxton on a piece of blotting paper) and of its construction (six months).
The reason, and the reason for its lasting architectural significance, is that Paxton's building is the first thoroughgoing example of prefabricated architecture (a concept perfectly suited to cast iron, and pioneered seventy years earlier for the bridge at Coalbrookdale).
The reason, and the reason for its lasting architectural significance, is that Paxton's building is the first thoroughgoing example of prefabricated architecture (a concept perfectly suited to cast iron, and pioneered seventy years earlier for the bridge at Coalbrookdale).
The statistics of the Crystal Palace are bewildering (3300 iron columns, 2150 iron girders, 250 miles of sash bar, 293,635 panes of glass), but the crucial detail is that these all conform to a basic 24-foot module. The manufacture of the pieces can be subcontracted to several foundries and glass factories; assembly on site is like putting together a giant's dolls' house. Hence the fact that this palace of glass is created, from scratch, in less than 200 days. As if to emphasize the point, it is dismantled in 1852 and moved to another site at Sydenham - where it stands until its contents catch fire in 1936.
The modular steel-frame tradition of late 20th-century architecture has in this building its most distinguished ancestor.
The modular steel-frame tradition of late 20th-century architecture has in this building its most distinguished ancestor.
This History is as yet incomplete.
This History is as yet incomplete.
Page
1
of
6