HISTORY OF THE INDUSTRIAL REVOLUTION
To AD 1750
Humanity's twin revolutions
Human society has passed through two huge and lasting changes which deserve the name revolution. The first, the Neolithic revolution, begins in 8000 BC and continues through thousands of years. Its effect is to settle people on the land. It makes peasant agriculture the standard everyday activity of the human species.
The second, the Industrial Revolution, gathers pace in the 18th century and is still developing today. It moves people from the countryside into rapidly expanding towns. It turns labour into a disciplined and mainly indoor activity, with an increasing distinction between owners, employers and managers on one side and workers on the other.
The second, the Industrial Revolution, gathers pace in the 18th century and is still developing today. It moves people from the countryside into rapidly expanding towns. It turns labour into a disciplined and mainly indoor activity, with an increasing distinction between owners, employers and managers on one side and workers on the other.
Elements characteristic of industrial society can be seen in isolated examples long before the 18th century. In 1378 the workers in Florence's cloth trade win temporary advantages through standing together in what would now be called industrial action. A Knitting machine invented in England in 1589 is so far ahead of its time that it can play a profitable role in factories two and three centuries later. And the development of Cloth mills in the late Middle Ages foreshadows the search for new sources of power in the Industrial Revolution.
Nevertheless there is one place and one time - England in the 18th century - in which these threads coalesce into a process of undeniable change.
Nevertheless there is one place and one time - England in the 18th century - in which these threads coalesce into a process of undeniable change.
Industrialization brings preliminary evils of exploitation, pollution and urban squalor, together with longer-term benefits in a general rise of living standards.
There are certain clear reasons why this process occurs first in 18th-century Britain. But once the pattern is established, and cheap manufactured goods begin to prevail in world markets, other regions become eager to follow suit when their own circumstances make it possible to do so. Just as the habit of settling and farming gradually permeated all regions of the world, so now - and much more rapidly - does an international tendency to crowd into cities and produce cheap manufactured goods.
There are certain clear reasons why this process occurs first in 18th-century Britain. But once the pattern is established, and cheap manufactured goods begin to prevail in world markets, other regions become eager to follow suit when their own circumstances make it possible to do so. Just as the habit of settling and farming gradually permeated all regions of the world, so now - and much more rapidly - does an international tendency to crowd into cities and produce cheap manufactured goods.
Britain's industrial advantages: 18th century AD
The conditions enabling Britain to pioneer the Industrial Revolution during the 18th century can be divided into two categories, natural and political.
On the natural side the country has in abundance three important commodities - water, iron and coal. Water in Britain's numerous hilly districts provides the power to drive mills in the early stages of industrializaton; the rivers, amplified from 1761 by a developing network of Canals, facilitate inland transport in an age where roads are only rough tracks; and the sea, never far from any part of Britain, makes transport of heavy goods easy between coastal cities.
On the natural side the country has in abundance three important commodities - water, iron and coal. Water in Britain's numerous hilly districts provides the power to drive mills in the early stages of industrializaton; the rivers, amplified from 1761 by a developing network of Canals, facilitate inland transport in an age where roads are only rough tracks; and the sea, never far from any part of Britain, makes transport of heavy goods easy between coastal cities.
The ability to make effective use of Britain's iron ore is greatly enhanced by technical advances in the early 18th century, associated particularly with the Darby family. And the abundant supplies of coal become of crucial importance in the second half of the century when steam power is successively applied to every branch of industry thanks to the efforts of Watt and boulton.
On the political front, the contribution of entrepreneurs such as Abraham Darby and Matthew Boulton is made possible by the changes resulting from the Revolution of 1688.
On the political front, the contribution of entrepreneurs such as Abraham Darby and Matthew Boulton is made possible by the changes resulting from the Revolution of 1688.
With royal power greatly reduced after 1688, and the nobility enjoying none of the privileges associated with France's ancien régime, a new middle class emerges more forcefully in Britain than elsewhere. There is money to be made, and members of this class are willing to back new inventions and mechanical improvements.
In this atmosphere exceptional men such as Richard Arkwright can rise through their own endeavours from low beginnings to exceptional wealth and prestige (though the duke of Bridgewater may justifiably insist that such flair is not limited to the middle classes).
In this atmosphere exceptional men such as Richard Arkwright can rise through their own endeavours from low beginnings to exceptional wealth and prestige (though the duke of Bridgewater may justifiably insist that such flair is not limited to the middle classes).
As a final ingredient in this promising blend of circumstances, Britain can offer its budding entrepreneurs an unusually large market. The Union in 1707 of Scotland and England removes internal tariff barriers. The developing British empire provides trading opportunities for much of the century in the American colonies - and when these are lost, begins to replace them with others in India.
And British control of the seas, increasingly established during the century, contributes to a general prosperity which supports the Industrial Revolution. Much of the profitable carrying trade in the world's commerce can be secured for British merchant vessels.
And British control of the seas, increasingly established during the century, contributes to a general prosperity which supports the Industrial Revolution. Much of the profitable carrying trade in the world's commerce can be secured for British merchant vessels.
Ironmasters of Coalbrookdale: 18th century AD
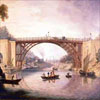
Until the early 18th century the working of iron has been restricted by a practical consideration. The smelting of iron requires large quantities of charcoal, with the result that ironworks are usually sited inaccessibly in the middle of forests. And charcoal is expensive.
In 1709 Abraham Darby, an ironmaster with a furnace at Coalbrookdale on the river Severn, discovers that coke can be used instead of charcoal for the smelting of pig iron (used for cast-iron products). This Severn region becomes Britain's centre of iron production in the early stages of the Industrial Revolution. Its pre-eminence is seen in the Darby family's own construction of the first Iron bridge, and in the achievements of John Wilkinson.
In 1709 Abraham Darby, an ironmaster with a furnace at Coalbrookdale on the river Severn, discovers that coke can be used instead of charcoal for the smelting of pig iron (used for cast-iron products). This Severn region becomes Britain's centre of iron production in the early stages of the Industrial Revolution. Its pre-eminence is seen in the Darby family's own construction of the first Iron bridge, and in the achievements of John Wilkinson.
Lancashire and cotton: 18th century AD
Just as the Severn gorge in Shropshire emerges as the centre of the iron industry, so Lancashire dominates in cotton goods. And textiles are the natural product to lead developments in the new Industrial Revolution.
Food and clothing are the two basic requirements for any population. Unlike food, cotton goods are sufficiently light and long-lasting to be easily transported to any market. The immediate purchasers are the rapidly growing population of Britain itself. But as soon as machines are developed which can slash the cost of production, it even becomes feasible to ship manufactured cotton goods for sale in regions such as India where the raw material has been produced.
Food and clothing are the two basic requirements for any population. Unlike food, cotton goods are sufficiently light and long-lasting to be easily transported to any market. The immediate purchasers are the rapidly growing population of Britain itself. But as soon as machines are developed which can slash the cost of production, it even becomes feasible to ship manufactured cotton goods for sale in regions such as India where the raw material has been produced.
Lancashire has certain natural advantages in cornering this lucrative trade. A moist climate makes it easier to work cotton threads, which become brittle if dry (the first reference to cotton goods being produced in the region is in 1641). Plentiful fast-flowing streams make it easy to provide water power for Mills. The area has a long textile tradition in the production of woollen goods (there is a mill for fulling wool in Manchester as early as 1282).
And above all Lancashire has, in Liverpool, one of Britain's two main 18th-century ports. It is rivalled only by Bristol as a base for the great East and West Indiamen which now ply regularly across the oceans.
And above all Lancashire has, in Liverpool, one of Britain's two main 18th-century ports. It is rivalled only by Bristol as a base for the great East and West Indiamen which now ply regularly across the oceans.
The rapid growth of the textile industry during the 18th century results from these advantages combined with a succession of mechanical inventions which speed up the processes of manufacture. Spinning and weaving, the two very ancient crafts involved in the production of textiles, are both well suited to relatively simple mechanization.
Weaving leads the way, with Kay's flying shuttle of 1733. Spinning at first struggles to keep up, and then does so very effectively with the innovations of Hargreaves in about 1764 and Crompton in 1779. Spinning wins the race in the application of Water power, in 1771. By 1787 there are some forty cotton Mills in Lancashire deriving their power from mill races.
Weaving leads the way, with Kay's flying shuttle of 1733. Spinning at first struggles to keep up, and then does so very effectively with the innovations of Hargreaves in about 1764 and Crompton in 1779. Spinning wins the race in the application of Water power, in 1771. By 1787 there are some forty cotton Mills in Lancashire deriving their power from mill races.
Kay's flying shuttle: AD 1733
1750-1800
Bridgewater Canal: AD 1759-1761
In 1759 a young self-taught engineer, James Brindley, is invited to visit the duke of Bridgewater. The duke is interested in improving the market for the coal from a local mine which he owns. He believes his coal will find customers if he can get it more cheaply into Manchester. He wants Brindley to build him a canal with a series of locks to get barges down to the river Irwell, about three miles from the mine.
Brindley proposes a much bolder scheme, declared by some to be impossible but accepted by the duke. He will construct a more level canal, with less need for time-wasting locks. He will carry it on an aqudeuct over the Irwell on a straight line to the heart of Manchester, ten miles away.
Brindley proposes a much bolder scheme, declared by some to be impossible but accepted by the duke. He will construct a more level canal, with less need for time-wasting locks. He will carry it on an aqudeuct over the Irwell on a straight line to the heart of Manchester, ten miles away.
On 17 July 1761 the first bargeload of coal is pulled along the completed canal. Brindley's aqueduct (replaced in 1894 by the present swing aqueduct) crosses the Irwell at Barton. The strange sight of a barge floating in a gutter high up in the air becomes one of the first great tourist attractions of the Industrial Revolution. The investment in this private canal rapidly pays off. The price of the duke's coal is halved in the Manchester market.
The Bridgewater canal is the first in Britain to run its entire length independently of any river. It is the start of the country's inland waterway systerm, for which Brindley himself will construct another 300 miles of canals.
The Bridgewater canal is the first in Britain to run its entire length independently of any river. It is the start of the country's inland waterway systerm, for which Brindley himself will construct another 300 miles of canals.
James Watt and the condenser: AD 1764-1769
In 1764 a model of a Newcomen steam engine is brought for repair to the young James Watt, who is responsible for looking after the instruments in the physics department of the university of Glasgow. In restoring it to working order, he is astonished at how much steam it uses and wastes.
The reason, he realizes, is that the machine's single cylinder is required to perform two opposing functions. It must receive the incoming steam at maximum pressure to force the piston up (for which it needs to be as hot as possible), and it must then condense the steam to form a vacuum to pull the cylinder down (for which it needs to be as cool as possible).
The reason, he realizes, is that the machine's single cylinder is required to perform two opposing functions. It must receive the incoming steam at maximum pressure to force the piston up (for which it needs to be as hot as possible), and it must then condense the steam to form a vacuum to pull the cylinder down (for which it needs to be as cool as possible).
The solution occurs to Watt when he is walking near Glasgow one Sunday in May 1765. The two functions could be separated by providing a chamber, outside the cylinder but connecting with it, in which a jet of cold water will condense the steam and cause the vacuum.
This chamber is the condenser, for which Watt registers a patent in 1769. The principle has remained an essential part of all subsequent steam engines. It is the first of three major improvements which Watt makes in the basic design of steam-driven machinery. The other two are the Double-acting engine and the Governor, developed in the 1780s.
This chamber is the condenser, for which Watt registers a patent in 1769. The principle has remained an essential part of all subsequent steam engines. It is the first of three major improvements which Watt makes in the basic design of steam-driven machinery. The other two are the Double-acting engine and the Governor, developed in the 1780s.
Early in the 1770s Watt goes into business with Matthew Boulton, an entrepreneur with a large factory at Soho near Birmingham. Boulton has the capacity to manufacture steam engines to Watt's patented design, and the first two are delivered to customers in 1776.
One of them, installed by Watt himself at John Wilkinson's ironworks at Broseley in Shropshire, is of special significance. Wilkinson is the only ironmaster in the country capable of producing cylinders of sufficiently accurate dimensions to deliver the potential benefits of Watt's improved engine.
One of them, installed by Watt himself at John Wilkinson's ironworks at Broseley in Shropshire, is of special significance. Wilkinson is the only ironmaster in the country capable of producing cylinders of sufficiently accurate dimensions to deliver the potential benefits of Watt's improved engine.
Hargreaves jenny and Cromptow's mule: AD 1764-1779
An accident is said to have given a Lancashire spinner, James Hargreaves, the idea for the first mechanical improvement of the spinning process. In about 1764 he notices an overturned spinning wheel which continues to turn with the spindle vertical rather than horizontal. This gives him the idea that several spindles could be worked simultaneously from a wheel in this position.
He develops a version with eight spindles for use by his own family, thus immediately raising their output eight times. News of this causes jealous local spinners to invade his house and smash his machines.
He develops a version with eight spindles for use by his own family, thus immediately raising their output eight times. News of this causes jealous local spinners to invade his house and smash his machines.
Hargreaves moves to Nottingham, where he sets up a small cotton-mill using his invention. It acquires the name of spinning jenny, traditionally explained as being the name of the daughter who gave Hargreaves the idea when she knocked over her spinning wheel. He patents his device in 1770. By the time of his death, in 1778, the latest versions of his machine work eighty spindles each - and there are said 20,000 jennies in use in the cottages and small factories of Britain.
This is still an entirely hand-operated mechanism. The next essential development is the application of power. This is solved by Richard Arkwright, who takes out a patent for his machine in 1769.
This is still an entirely hand-operated mechanism. The next essential development is the application of power. This is solved by Richard Arkwright, who takes out a patent for his machine in 1769.
Arkwright's innovation is in drawing out the cotton by means of rollers before it is twisted into yarn. He succeeds first with a machine worked by a horse, but two years later - in 1771 - he successfully applies water power, with the result that his invention becomes known as the water frame. It is in place just in time for an immense new expansion of the cotton industry after a high tax on pure-cotton fabrics (aimed at calicoes imported from India) is reduced in 1774.
Arkwright's machines are suitable for spinning the strong yarn required for the warp of the Woven cloth. They are less good at the finer material needed for the weft. Yet conversely, Hargreaves' spinning jenny is only suitable for the weft.
Arkwright's machines are suitable for spinning the strong yarn required for the warp of the Woven cloth. They are less good at the finer material needed for the weft. Yet conversely, Hargreaves' spinning jenny is only suitable for the weft.
The technologies of Arkwright and Hargreaves therefore complement each other for a few years until the merits of each are combined by Samuel Crompton, a worker in a Lancashire spinning mill. In doing so he takes the final step in the spinning technology of the early Industrial Revolution.
Crompton observes the tendency of the spinning jenny to break the yarn, and he resolves to improve this aspect of the process. He does so in a machine which he perfects in 1779.
Crompton observes the tendency of the spinning jenny to break the yarn, and he resolves to improve this aspect of the process. He does so in a machine which he perfects in 1779.
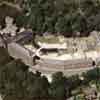
Crompton's machine combines the principles of Hargreaves' jenny and of Arkwright's water frame. The name which it acquires - Crompton's mule - is a pun on that fact. As the offspring of a jenny (a female donkey) and of another creature, the new arrival is clearly a mule.
Crompton's machine is capable of spinning almost every kind of yarn at considerable speed. The flying shuttle in the 1750s put pressure on the spinners to catch up. Now the mule challenges the weavers. They respond in 1785 with the first water-driven power loom, invented by Edmund Cartwright after visiting Arkwright's mills at Cromford. With all this technology in place, the pressure is now on the suppliers of raw Cotton in america.
Crompton's machine is capable of spinning almost every kind of yarn at considerable speed. The flying shuttle in the 1750s put pressure on the spinners to catch up. Now the mule challenges the weavers. They respond in 1785 with the first water-driven power loom, invented by Edmund Cartwright after visiting Arkwright's mills at Cromford. With all this technology in place, the pressure is now on the suppliers of raw Cotton in america.
Ironbridge: AD 1779
In the space of a few months in 1779 the world's first iron bridge, with a single span of over 100 feet, is erected for Abraham darby (the third of that name) over the Severn just downstream from Coalbrookdale. Work has gone on for some time in building the foundations and casting the huge curving ribs. But in this new technology little time need be spent in assembling the parts - which amount, it is proudly announced, to 378 tons 10 cwt. of metal.
The lightness of the structure strikes all observers. An early visitor comments: 'though it seems like network wrought in iron, it will be uninjured for ages.' It is uninjured still. A great tradition, bringing marvels such as the Crystal palace, begins in this industrial valley.
The lightness of the structure strikes all observers. An early visitor comments: 'though it seems like network wrought in iron, it will be uninjured for ages.' It is uninjured still. A great tradition, bringing marvels such as the Crystal palace, begins in this industrial valley.
This History is as yet incomplete.
Machine tools gun barrels and cylinders: AD 1774-1800
Richard Arkwright entrepreneur: AD 1767-1792

By the 1780s, on the eve of the French Revolution, Britain is a society profoundly changed from a century earlier. The form of monarchy characterized by the Stuarts, and still practised by the Bourbon rulers in France, has given way to different structures. There is now political power in middle-class hands. And new opportunities are available in the developing Industrial Revolution.
There is no more striking example of this flexible society, in which merit can find its own rewards, than the career of Richard Arkwright. Born the youngest of seven children of a barber and wigmaker, he dies sixty years later immensely wealthy and a knight of the realm.
There is no more striking example of this flexible society, in which merit can find its own rewards, than the career of Richard Arkwright. Born the youngest of seven children of a barber and wigmaker, he dies sixty years later immensely wealthy and a knight of the realm.
Arkwright begins his career travelling the country in his father's trade, buying hair for wigs and dying it by his own secret process. But soon he becomes interested in spinning. In 1767 he begins to construct a spinning machine. In 1769 he patents it and sets up a mill in Nottingham where his machine is worked by a horse.
Two years later Arkwright takes several steps of great significance. He raises capital to build an entirely new mill at Cromford, on the river Derwent in Derbyshire. He successfully adapts his spinning machine, making it work by the much greater power of the river and a mill wheel. And he builds cottages to house workers in the immediate vicinity.
Two years later Arkwright takes several steps of great significance. He raises capital to build an entirely new mill at Cromford, on the river Derwent in Derbyshire. He successfully adapts his spinning machine, making it work by the much greater power of the river and a mill wheel. And he builds cottages to house workers in the immediate vicinity.
Arkwright thus creates the factory environment. His industrial workers are a community centred on the factory - in strong contrast to the traditional working life of peasants, dependent on the fields and the seasons.
Within the factory, Arkwright's employees specialize in different tasks, each providing his or her own particular service for the relentlessly demanding machines. Discipline is essential if this system is to work, for the machines cannot be left untended. But it is no longer the variable discipline of sunrise and harvest. It is the inflexible and potentially harsh pressure of clock and overseer.
Within the factory, Arkwright's employees specialize in different tasks, each providing his or her own particular service for the relentlessly demanding machines. Discipline is essential if this system is to work, for the machines cannot be left untended. But it is no longer the variable discipline of sunrise and harvest. It is the inflexible and potentially harsh pressure of clock and overseer.
Arkwright's factory system works brilliantly - and in its early small-scale river-based form the environment of industry has considerable picturesque appeal, as Arkwright's surviving mill at Cromford still demonstrates.
Arkwright builds cotton mills on suitable rivers elsewhere in the country, as far away as Scotland. By 1782, just fifteen years after his first attempt to build a spinning machine, the great entrepreneur has a capital of some £200,000 and is employing 5000 workers. And British society welcomes this rapidly self-made man. In 1786 he receives a knighthood. In the following year he is appointed High Sheriff of Derbyshire.
Arkwright builds cotton mills on suitable rivers elsewhere in the country, as far away as Scotland. By 1782, just fifteen years after his first attempt to build a spinning machine, the great entrepreneur has a capital of some £200,000 and is employing 5000 workers. And British society welcomes this rapidly self-made man. In 1786 he receives a knighthood. In the following year he is appointed High Sheriff of Derbyshire.
Derby's great painter of the period, Joseph Wright, records features of this impressive story. In 1783 he paints a view of Cromford Mill by moonlight, contributing to a growing perception that industry and its processes provide a romantic subject. In 1789 Wright provides a portrait of the great industrialist. He sits alone, appearing prosperous but slightly gross, in a room decorated only by a model of his spinning machine.
In the following year Joseph Wright paints Arkwright's son, daughter-in-law and grandchildren in three group portraits. They look like the most elegant and refined of aristocrats, to the manner born - compelling evidence of the new flexibility of English society when William Pitt becomes prime minister.
In the following year Joseph Wright paints Arkwright's son, daughter-in-law and grandchildren in three group portraits. They look like the most elegant and refined of aristocrats, to the manner born - compelling evidence of the new flexibility of English society when William Pitt becomes prime minister.
Double-acting engine and governor: AD 1782-1787
Just as James Watt applied a rational approach to improve the efficiency of the steam engine with the Condenser, so now he takes a logical step forward in a modification patented in 1782. His new improvement is the double-acting engine.
Watt observes that the steam is idle for half of each cycle. During the downward stroke, when the vacuum is exerting atmospheric force on the piston, the valve between boiler and cylinder is closed. Watt takes the simple step of diverting the steam during this part of the cycle to the upper part of the cylinder, where it joins with the atmospheric pressure in forcing the cylinder down - and thus doubles its effective action.
Watt observes that the steam is idle for half of each cycle. During the downward stroke, when the vacuum is exerting atmospheric force on the piston, the valve between boiler and cylinder is closed. Watt takes the simple step of diverting the steam during this part of the cycle to the upper part of the cylinder, where it joins with the atmospheric pressure in forcing the cylinder down - and thus doubles its effective action.
The most elegant contraption devised by Watt is in use from 1787. It is the governor - the first example of the type of controlling device required in industrial automation, and a feature of all steam engines since Watt's time.
Watt's governor consists of two arms, hinged on a central pivot and rotated by the action of the steam engine. Each arm has a heavy ball at the end. As the speed increases, centrifugal force moves the balls and the arms outwards. This action narrows the aperture of a valve controlling the flow of steam to the engine. As the power is slowly cut off, the speed of the engine reduces and the balls subside nearer to the central column - thus slightly opening the valve again in a permanent process of adjustment.
Watt's governor consists of two arms, hinged on a central pivot and rotated by the action of the steam engine. Each arm has a heavy ball at the end. As the speed increases, centrifugal force moves the balls and the arms outwards. This action narrows the aperture of a valve controlling the flow of steam to the engine. As the power is slowly cut off, the speed of the engine reduces and the balls subside nearer to the central column - thus slightly opening the valve again in a permanent process of adjustment.
Watt's many improvements to the steam engine leave it poised to undertake a whole new range of tasks. Its new efficiency means that it can become mobile. Each engine can now generate more power than is required merely to move itself.
By the time of his death in 1819, in quiet retirement near Birmingham, Watt has seen the introduction of commercially successful steam boats and the dawn of the railway age. In each case the vehicles are powered by engines of the type which he has developed.
By the time of his death in 1819, in quiet retirement near Birmingham, Watt has seen the introduction of commercially successful steam boats and the dawn of the railway age. In each case the vehicles are powered by engines of the type which he has developed.
This History is as yet incomplete.
Puddling and rolling: AD 1783-1784
In successive years Henry Cort, an ironmaster with a mill near Fareham in Hampshire, patents two processes of lasting significance in the story of metallurgy.
One is the technique which becomes known as puddling, for which Cort patents a machine in 1784. Cort's innovation is a furnace which shakes the molten iron so that air mingles with it. Oxygen combines with carbon in the metallic compond, leaving almost pure iron. Unlike the brittle pig iron (or cast iron), this purer metal is malleable. Capable of being hammered and shaped, it is a much more useful metal in industrial processes than cast iron.
One is the technique which becomes known as puddling, for which Cort patents a machine in 1784. Cort's innovation is a furnace which shakes the molten iron so that air mingles with it. Oxygen combines with carbon in the metallic compond, leaving almost pure iron. Unlike the brittle pig iron (or cast iron), this purer metal is malleable. Capable of being hammered and shaped, it is a much more useful metal in industrial processes than cast iron.
In the previous year Cort has also patented a machine for drawing out red-hot lumps of purefied metal between grooved rollers, turning them into manageable bars without the laborious process of hammering. His device is the origin of the rolling mills which subsequently become the standard factories of the steel industry.
Cort's subsequent career exemplifies the risks involved in the entrepreneurial excitements of the Industrial Revolution. After spending all his own money on his inventions, he raises further capital from the deputy-paymaster of the navy. It turns out to have been embezzled. Cort is ruined before his inventions bring him a profit.
Cort's subsequent career exemplifies the risks involved in the entrepreneurial excitements of the Industrial Revolution. After spending all his own money on his inventions, he raises further capital from the deputy-paymaster of the navy. It turns out to have been embezzled. Cort is ruined before his inventions bring him a profit.
This History is as yet incomplete.
Cotton gin: AD 1793
The mechanization of spinning and weaving in England, between 1733 and 1785, greatly speeds up the industrial process and rapidly leads to a shortage of cotton. During most of the century the bulk of raw cotton arriving at Liverpool for the Lancashire mills is from India. The cotton grown in the southern states of America is commercially less viable because it is short-fibred.
The cotton fibres, which will be spun into cotton, have to be separated from the seeds which they protect and enmesh. This process, known as cotton picking, is done entirely by hand. The short fibres make it a slow and expensive task.
The cotton fibres, which will be spun into cotton, have to be separated from the seeds which they protect and enmesh. This process, known as cotton picking, is done entirely by hand. The short fibres make it a slow and expensive task.
In 1793 Eli Whitney, a graduate of Yale, invents a machine which solves this problem. It consists of a hand-turned roller with projecting spikes. Each spike passes through a slot in a grid, wide enough to allow the spike to drag the cotton fibres through but too narrow for the cotton seeds to pass. They fall out into a separate container, while a revolving brush cleans the fibres, or lint, off the spikes.
Whitney's machine immediately trebles the speed at which cotton can be ginned, with major effects on the economy of the southern states of America. About forty times as much cotton (now established as 'king cotton') is produced in 1810 as in 1793. Vast new areas are taken in hand as plantations. The demand for slaves increases accordingly.
Whitney's machine immediately trebles the speed at which cotton can be ginned, with major effects on the economy of the southern states of America. About forty times as much cotton (now established as 'king cotton') is produced in 1810 as in 1793. Vast new areas are taken in hand as plantations. The demand for slaves increases accordingly.
19th century and beyond
Pont Cysyllte: AD 1795-1805
In 1795 Thomas Telford applies cast-iron technology in a bold new context. In 1793 he has been appointed engineer and architect to the Shropshire Union canal, which is to link the Mersey with the Severn. Near Llangollen the proposed route crosses the Dee valley, which is more than 300 yards wide and drops down about 120 feet to the river level below.
The number of locks needed to get a barge down and up again would represent a costly delay for the bargees. Yet an aqueduct of this height and length is a daunting project. The valley is much wider and deeper than the one spanned by Brindley in his heavily buttressed aqueduct at Barton. But Telford accepts the challenge.
The number of locks needed to get a barge down and up again would represent a costly delay for the bargees. Yet an aqueduct of this height and length is a daunting project. The valley is much wider and deeper than the one spanned by Brindley in his heavily buttressed aqueduct at Barton. But Telford accepts the challenge.
Telford constructs at Pont Cysyllte what is in effect an enormous cast-iron gutter. Cast to the correct curves and then welded together, Telford's plates combine to form a channel which is nearly 12 feet wide, with a path alongside for the carthorse. The metal is much lighter than the thick layer of pounded clay and sand used by Brindley to contain the water of the Bridgewater canal. So Telford's aqueduct can be a slender structure of nineteen tall stone arches.
Pont Cysyyllte is ready for the first barge to make the journey across the valley in 1805. Walter Scott describes it as 'the most impressive work of art' which he has ever seen.
Pont Cysyyllte is ready for the first barge to make the journey across the valley in 1805. Walter Scott describes it as 'the most impressive work of art' which he has ever seen.
The growth of industrial cities: 18th - 19th century AD

The availability of work in Britain's mills and factories, particularly after the introduction of Steam power, has the effect of drawing ever-increasing numbers of people from the countryside into rapidly expanding cities. Manchester and the closely related town of Salford have 25,000 inhabitants between them in 1772. In 1821 the joint population is 181,000. By 1851 this conurbation has grown to 455,000.
The growth of Manchester's Textile industry brings equivalent prosperity to the nearby port of Liverpool - just in time since the Slave trade, the previous source of Liverpool's wealth, is made illegal in 1807. Cotton saves the day. Eight new docks are built in Liverpool between 1815 and 1835.
The growth of Manchester's Textile industry brings equivalent prosperity to the nearby port of Liverpool - just in time since the Slave trade, the previous source of Liverpool's wealth, is made illegal in 1807. Cotton saves the day. Eight new docks are built in Liverpool between 1815 and 1835.
The amount of raw cotton brought ashore in Liverpool shows a threefold increase between 1820 and 1850, from half a million bales a year to 1.5 million. There is a comparable rise in the population - with a leap of 60% in a single decade, the 1840s, from 250,000 to 400,000 inhabitants.
The other great industrial city of the era, Birmingham, starts from a lower base. Its population increases from 86,000 to 233,000 between 1801 and 1851. Birmingham's interests are broader than those of Lancashire, where textiles predominate. Birmingham is blessed with an abundance of coal, iron and wood in the immediate neighbourhood, and with a position at the very heart of England.
The other great industrial city of the era, Birmingham, starts from a lower base. Its population increases from 86,000 to 233,000 between 1801 and 1851. Birmingham's interests are broader than those of Lancashire, where textiles predominate. Birmingham is blessed with an abundance of coal, iron and wood in the immediate neighbourhood, and with a position at the very heart of England.
Birmingham's real potential is realized only with the arrival of the railway. The line to London is completed in 1838. By then the city's workshops, specializing in metal-based industries, are ready to supply a wider market. A French visitor in 1835, Alexis de Tocqueville, describes the place as 'an immense workshop, a huge forge', where one sees only 'busy people and faces brown with smoke' and hears 'nothing but the sound of hammers and the whistle of Steam escaping from boilers'.
To a detached observer the Industrial Revolution can seem Romantic in the 1780s and fascinatingly strange in the 1830s. But it is also becoming evident that it creates an environment in which it can be extremely unpleasant to work.
To a detached observer the Industrial Revolution can seem Romantic in the 1780s and fascinatingly strange in the 1830s. But it is also becoming evident that it creates an environment in which it can be extremely unpleasant to work.
New Lanark and elsewhere: AD 1800-1847
In 1800 Robert Owen takes charge of a cotton mill at New Lanark on the Clyde. It has been previously owned by his father-in-law, who established it in 1785 in partnership with Arkwright. It is therefore a thoroughly modern enterprise, well run by the standards of the time. But the idealistic young Owen is distressed by the conditions in which the employees and their families (some 2000 people in all) live and work.
Seeing ignorance, crime and drunkenness in the community, he blames it not on the workers but on their environment. And he considers the environment at New Lanark, or in any other factory, to be the direct result of the mill owners' overriding concern to make money.
Seeing ignorance, crime and drunkenness in the community, he blames it not on the workers but on their environment. And he considers the environment at New Lanark, or in any other factory, to be the direct result of the mill owners' overriding concern to make money.
For the first time, in this perception, the ideals of socialism are directly opposed to the tenets of Capitalism. The two great rivals of 20th-century politics discover each other.
Owen's reforms make New Lanark an essential port of call for anyone interested in social reform. Visitors admire the high standards in housing and the conditions in the factory. They note that goods are sold in the village shop at almost cost price. They see the care shown for the health of the families and the education of their children (Britain's first primary school is opened here in 1812). New Lanark becomes, and is recognized to be, a model industrial community.
Owen's reforms make New Lanark an essential port of call for anyone interested in social reform. Visitors admire the high standards in housing and the conditions in the factory. They note that goods are sold in the village shop at almost cost price. They see the care shown for the health of the families and the education of their children (Britain's first primary school is opened here in 1812). New Lanark becomes, and is recognized to be, a model industrial community.
Yet New Lanark is also a conventional business, making a good profit for its owners. Owen begins to dream of more utopian ways of solving society's ills. He promotes the idea of self-contained communities of agricultural workers and craftsmen, owning everything in common including their land. With no capitalist owner to cream off the profit, he imagines such communities being so successful that they soon become the standard form of human society.
He proves less effective as utopian theorist than as benevolent mill owner. Four Owenite communities are founded between 1825 and 1839 (the best known is at New Harmony in Indiana). Squabbles and bankruptcy finish off every one of them within a very few years.
He proves less effective as utopian theorist than as benevolent mill owner. Four Owenite communities are founded between 1825 and 1839 (the best known is at New Harmony in Indiana). Squabbles and bankruptcy finish off every one of them within a very few years.
Robert Owen severs his connection with New Lanark in 1829, the very year in which the trials at Rainhill introduce the railway era. The replacement of canals by railways for the transport of freight greatly speeds up the process of the Industrial Revolution, and makes possible the growth of the great manufacturing cities of the 19th century.
New Lanark, an elegant and isolated experiment in the countryside, is not a viable model in these circumstances. More effective in the long run, as a way of restraining the tendency of employers to exploit workers, is the painstaking process of welfare legislation.
New Lanark, an elegant and isolated experiment in the countryside, is not a viable model in these circumstances. More effective in the long run, as a way of restraining the tendency of employers to exploit workers, is the painstaking process of welfare legislation.
Owen's community at New Harmony lasts just two years, from 1825 to 1827, but it is followed in the 1840s by many other similar experiments in north America. They are based posthumously on the ideas of the French social theorist, Charles Fourier, who has proposed an ideal community which he calls a 'phalanx'. Each phalanx is to include a balanced mix of workers, combining all the necessary skills. A community of 1620 people is suggested as the ideal size.
As many as twenty-eight Fourier phalanxes are founded in the USA. Most of them soon collapse. The one which makes the movement famous, Brook Farm near Boston, lasts from 1841 to 1847. But in this same decade two young men in Paris are evolving a more ruthless concept of socialism.
As many as twenty-eight Fourier phalanxes are founded in the USA. Most of them soon collapse. The one which makes the movement famous, Brook Farm near Boston, lasts from 1841 to 1847. But in this same decade two young men in Paris are evolving a more ruthless concept of socialism.
Factories and slums: 19th - 20th century AD
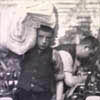
In any peasant community children work in the fields. As families move in from the countryside to work in Britain's developing industrial cities, there is nothing intrinsically strange about children joining their parents in the factories. And the entrepreneurs who own the factories welcome a supply of labour trapped by economic circumstances into accepting long hours and low pay.
The living conditions of the poor in any rapidly growing city, without sanitation, are invariably worse than the condition of peasants in the countryside. But in Britain in the early 19th century it is exploitation within the factories which prompts the first measures of reform.
The living conditions of the poor in any rapidly growing city, without sanitation, are invariably worse than the condition of peasants in the countryside. But in Britain in the early 19th century it is exploitation within the factories which prompts the first measures of reform.
The first Factory Act, in 1802, introduces a regulation which by later standards seems astonishing. It limits the amount of time which a child may work in a factory to twelve hours a day.
After much opposition the reformers achieve significant improvements in the Factory Act of 1833. Children under nine are now not to work at all. Those aged between nine and thirteen are limited to eight hours of work and must be given two hours of education each day (this is the first small step towards compulsory education in Britain). And an inspectorate is set up for the factories, albeit initially with only four inspectors for the entire country.
After much opposition the reformers achieve significant improvements in the Factory Act of 1833. Children under nine are now not to work at all. Those aged between nine and thirteen are limited to eight hours of work and must be given two hours of education each day (this is the first small step towards compulsory education in Britain). And an inspectorate is set up for the factories, albeit initially with only four inspectors for the entire country.
The last significant regulation of hours of work is achieved in the Ten Hour Act of 1847, which stipulates that number of hours as the maximum working day for women and children in the nation's factories and textile mills. This act is largely the achievement of Lord Shaftesbury, who is responsible also for the Mines Act of 1842. This makes it illegal for women of any age and for boys under thirteen to be employed underground.
By the mid-century Shaftesbury is much concerned with the condition of London slums, campaigning actively for improvements in housing and public sanitation. In the 20th century environmental pollution comes to be seen as another deficit to be charged against the Industrial Revolution.
By the mid-century Shaftesbury is much concerned with the condition of London slums, campaigning actively for improvements in housing and public sanitation. In the 20th century environmental pollution comes to be seen as another deficit to be charged against the Industrial Revolution.
Industrialization, with its blend of benefits and drawbacks, spreads gradually round the world from its first manifestation in Britain. When a developing country has an adequate transport system, and the ability to provide the starting costs of industrial enterprises, it can begin to manufacture its own goods, from its own raw materials, rather than buying them from a more advanced economy. In certain industries the cheap labour of a developing economy can soon give a competitive edge in world markets.
Exploitation and slums remain characteristic of the Industrial Revolution anywhere in the world. But gradually, along with the pain and the misery, the average standard of living rises in any nation which takes this familiar path.
Exploitation and slums remain characteristic of the Industrial Revolution anywhere in the world. But gradually, along with the pain and the misery, the average standard of living rises in any nation which takes this familiar path.
Sections missing
Sections are as yet missing at this point
Electric and Electronic Revolutions: 20th century AD
The 20th century provides two further turning points in human social development which historians of the future may judge of equal significance to the Neolithic and Industrial Revolutions. The two may eventually seem to merge as a single revolution, since both are made possible by the discovery of electricity.
But from our closer perspective there seems an intrinsic difference between the Electric Revolution (by now a century old and familiar in its main applications) and the Electronic Revolution - which first impinges on the general public in the 1990s and still retains, in the 21st century, an unimaginable potential for transforming human life.
But from our closer perspective there seems an intrinsic difference between the Electric Revolution (by now a century old and familiar in its main applications) and the Electronic Revolution - which first impinges on the general public in the 1990s and still retains, in the 21st century, an unimaginable potential for transforming human life.
Page
1
of
3