HISTORY OF METALLURGY
The early centuries
A magic material
No substance has been as important as metal in the story of man's control of his environment. Advances in agriculture, warfare, transport, even cookery are impossible without metal. So is the entire Industrial Revolution, from steam to electricity.
Nature entices man into the adventure of metallurgy by an initial gift of an almost magic charm. Gold, the most attractive and precious of metals in every society, is also the easiest for primitive man to acquire. Gold is bright, incorruptible, malleable, and appears in pure form in the beds of streams. Once seen, acquiring it is just a matter of picking it up. Nuggets of this gleaming substance must often have been kept and treasured.
Nature entices man into the adventure of metallurgy by an initial gift of an almost magic charm. Gold, the most attractive and precious of metals in every society, is also the easiest for primitive man to acquire. Gold is bright, incorruptible, malleable, and appears in pure form in the beds of streams. Once seen, acquiring it is just a matter of picking it up. Nuggets of this gleaming substance must often have been kept and treasured.
Pure gold also has the quality of softness. It can be easily shaped by hammering, but this malleability makes it useless for practical purposes. It begins as it has continued - a luxury item. The earliest surviving gold jewellery is from Egypt in about 3000 BC.
By that time people have long discovered an everyday use for another metal which exists in nature in a pure form, and which can also be bashed into new shapes - with less ease than gold, for it is much harder, but with more practical results. This metal is copper.
By that time people have long discovered an everyday use for another metal which exists in nature in a pure form, and which can also be bashed into new shapes - with less ease than gold, for it is much harder, but with more practical results. This metal is copper.
The age of copper: from 7000 BC
From about 7000 BC a few neolithic communities begin hammering copper into crude knives and sickles, which work as well as their stone equivalents and last far longer. Some of the earliest implements of this kind have been found in eastern Anatolia.
This intermediate period between the Stone age (when all weapons and tools are of flint) and the first confident metal technology (the Bronze age) has been given a name deriving from the somewhat awkward combination of materials. It is called the Chalcolithic Period, from the Greek chalcos 'copper' and lithos 'stone'.
This intermediate period between the Stone age (when all weapons and tools are of flint) and the first confident metal technology (the Bronze age) has been given a name deriving from the somewhat awkward combination of materials. It is called the Chalcolithic Period, from the Greek chalcos 'copper' and lithos 'stone'.
An accident, probably frequent, reveals another of nature's useful secrets. A nugget of pure copper, or perhaps a finished copper tool, falls into the hot camp fire. The copper melts. When it cools, it is found to have solidified in a new shape.
And the magic of fire has yet more to offer. Certain kinds of bright blue or green stones are attractive enough to collect for their own sake. It turns out that when such stones are heated to a high temperature, liquid metal flows from them. They are azurite and malachite, two of the ores of copper.
And the magic of fire has yet more to offer. Certain kinds of bright blue or green stones are attractive enough to collect for their own sake. It turns out that when such stones are heated to a high temperature, liquid metal flows from them. They are azurite and malachite, two of the ores of copper.
The use of fire thus makes possible two significant new steps in the development of metallurgy: the casting of metal, by pouring it into prepared moulds; and the smelting of mineral ores to extract metal. Objects made from smelted copper, from as early as 3800 BC, are known in Iran.
Many mineral ores are found on the surface of the earth, in outcrops of rock. Chipping away at them, to pursue the metal-bearing lode down below the surface, leads inevitably to another technological advance - the development of mining.
Many mineral ores are found on the surface of the earth, in outcrops of rock. Chipping away at them, to pursue the metal-bearing lode down below the surface, leads inevitably to another technological advance - the development of mining.
The first miners: from 4000 BC
By 4000 BC deep shafts are cut into the hillside at Rudna Glava, in the Balkans, to excavate copper ore. This robbing of the earth's treasures is carried out with due solemnity. Fine pots, bearing produce from the daylight world, are placed in the mines as a form of recompense to propitiate the spirits of the dark interior of the earth.
By about 3800 BC copper mines are also worked in the Sinai peninsula. Crucibles found at the site reveal that smelting is carried out as part of the mining process.
By about 3800 BC copper mines are also worked in the Sinai peninsula. Crucibles found at the site reveal that smelting is carried out as part of the mining process.
The age of bronze: from 2800 BC
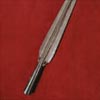
Sometimes the ores of copper and tin are found together, and the casting of metal from such natural alloys may have provided the accident for the next step forward in metallurgy. It is discovered that these two metals, cast as one substance, are harder than either metal on its own.
The cast alloy of copper and tin is bronze, a substance so useful to human beings that an entire period of early civilization has become known as the Bronze Age. A bronze blade will take a sharper edge than copper and will hold it longer. And bronze ornaments and vessels can be cast for a wide variety of purposes.
The cast alloy of copper and tin is bronze, a substance so useful to human beings that an entire period of early civilization has become known as the Bronze Age. A bronze blade will take a sharper edge than copper and will hold it longer. And bronze ornaments and vessels can be cast for a wide variety of purposes.
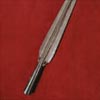
The technology of bronze is first developed in the Middle East. Bronze is in use in Sumer, at Ur, in around 2800 BC, and in Anatolia shortly afterwards. It then spreads spasmodically. It appears in the Indus valley in about 2500 BC, and progresses westwards through Europe from about 2000. At much the same time it is found in crude form in China, where it later achieves an unprecedented level of sophistication. From about 1500 BC the Shang dynasty produces bronze objects of exceptional brilliance.
In all these regions it is the rulers who use bronze, as a luxury for themselves or as a weapon for their armies. For ordinary people the Stone Age survives well into the Bronze age.
In all these regions it is the rulers who use bronze, as a luxury for themselves or as a weapon for their armies. For ordinary people the Stone Age survives well into the Bronze age.
As the most valuable of commodities (in addition to being compact and easily portable), metals are a great incentive to trade. The extensive deposits of copper on Cyprus bring the island much wealth from about 3000 BC (Cyprus, in Latin, gives copper its name - cyprium corrupted to cuprum).
Later, when the much scarcer commodity of tin is required to make bronze, even distant Cornwall becomes - by the first millennium BC - a major supplier of the needs of Bronze age Europe.
Later, when the much scarcer commodity of tin is required to make bronze, even distant Cornwall becomes - by the first millennium BC - a major supplier of the needs of Bronze age Europe.
The age of iron: from 1500 BC
The next great development in metallurgy involves a metal which is the most abundant in the earth's surface but which is much more difficult to work than copper or tin. It is iron, with a melting point too high for primitive furnaces to extract it in pure form from its ore. The best that can be achieved is a cluster of globules of iron mixed with sludgy impurities. This unpromising substance can be turned into a useful metal by repeated heating and hammering, until the impurities are literally forced out.
A few iron objects dating from before 2000 BC have been found (beads, a ring, some blades), but it is not until about 1500 BC that the working of iron is done anywhere on a regular basis.
A few iron objects dating from before 2000 BC have been found (beads, a ring, some blades), but it is not until about 1500 BC that the working of iron is done anywhere on a regular basis.
The magic of iron: from 1500 BC
The Hittites are the first people to work iron, in Anatolia from about 1500 BC. In its simple form iron is less hard than bronze, and therefore of less use as a weapon, but it seems to have had an immediate appeal - perhaps as the latest achievement of technology (with the mysterious quality of being changeable, through heating and hammering), or from a certain intrinsic magic (it is the metal in meteorites, which fall from the sky).
Quite how much value is attached to iron can be judged from a famous letter of about 1250 BC, written by a Hittite king to accompany an iron dagger-blade which he is sending to a fellow monarch (see Letter from a Hittite king).
Quite how much value is attached to iron can be judged from a famous letter of about 1250 BC, written by a Hittite king to accompany an iron dagger-blade which he is sending to a fellow monarch (see Letter from a Hittite king).
The discovery of steel: 11th century BC
By the 11th century BC it has been discovered that iron can be much improved. If it is reheated in a furnace with charcoal (containing carbon), some of the carbon is transferred to the iron. This process hardens the metal; and the effect is considerably greater if the hot metal is rapidly reduced in temperature, usually achieved by quenching it in water.
The new material is steel. It can be worked (or 'wrought') just like softer iron, and it will keep a finer edge, capable of being honed to sharpness. Gradually, from the 11th century onwards, steel replaces bronze weapons in the Middle East, birthplace of the Iron Age. It becomes essential, from now on, to have a good steel blade rather than a soft and indifferent one.
The new material is steel. It can be worked (or 'wrought') just like softer iron, and it will keep a finer edge, capable of being honed to sharpness. Gradually, from the 11th century onwards, steel replaces bronze weapons in the Middle East, birthplace of the Iron Age. It becomes essential, from now on, to have a good steel blade rather than a soft and indifferent one.
Cast iron in the east: 513 BC
Thus far in the story iron has been heated and hammered, but never melted. Its melting point (1528°C) is too high for primitive furnaces, which can reach about 1300°C and are adequate for copper (melting at 1083°C). This limitation is overcome when the Chinese develop a furnace hot enough to melt iron, enabling them to produce the world's first cast iron - an event traditionally dated in the Chinese histories to 513 BC.
In this they are a thousand and more years ahead of the western world. The first iron foundry in England, for example, dates only from AD 1161. By that time the Chinese have already pioneered the structural use of cast iron, using it sometimes for the pillars of full-size pagodas.
In this they are a thousand and more years ahead of the western world. The first iron foundry in England, for example, dates only from AD 1161. By that time the Chinese have already pioneered the structural use of cast iron, using it sometimes for the pillars of full-size pagodas.
Modern period
Ironmasters of Coalbrookdale: 18th century AD
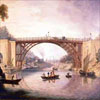
Until the early 18th century the working of iron has been restricted by a practical consideration. The smelting of iron requires large quantities of charcoal, with the result that ironworks are usually sited inaccessibly in the middle of forests. And charcoal is expensive.
In 1709 Abraham Darby, an ironmaster with a furnace at Coalbrookdale on the river Severn, discovers that coke can be used instead of charcoal for the smelting of pig iron (used for cast-iron products). This Severn region becomes Britain's centre of iron production in the early stages of the Industrial Revolution. Its pre-eminence is seen in the Darby family's own construction of the first Iron bridge, and in the achievements of John Wilkinson.
In 1709 Abraham Darby, an ironmaster with a furnace at Coalbrookdale on the river Severn, discovers that coke can be used instead of charcoal for the smelting of pig iron (used for cast-iron products). This Severn region becomes Britain's centre of iron production in the early stages of the Industrial Revolution. Its pre-eminence is seen in the Darby family's own construction of the first Iron bridge, and in the achievements of John Wilkinson.
Ironbridge: AD 1779
In the space of a few months in 1779 the world's first iron bridge, with a single span of over 100 feet, is erected for Abraham darby (the third of that name) over the Severn just downstream from Coalbrookdale. Work has gone on for some time in building the foundations and casting the huge curving ribs. But in this new technology little time need be spent in assembling the parts - which amount, it is proudly announced, to 378 tons 10 cwt. of metal.
The lightness of the structure strikes all observers. An early visitor comments: 'though it seems like network wrought in iron, it will be uninjured for ages.' It is uninjured still. A great tradition, bringing marvels such as the Crystal palace, begins in this industrial valley.
The lightness of the structure strikes all observers. An early visitor comments: 'though it seems like network wrought in iron, it will be uninjured for ages.' It is uninjured still. A great tradition, bringing marvels such as the Crystal palace, begins in this industrial valley.
This History is as yet incomplete.
Puddling and rolling: AD 1783-1784
In successive years Henry Cort, an ironmaster with a mill near Fareham in Hampshire, patents two processes of lasting significance in the story of metallurgy.
One is the technique which becomes known as puddling, for which Cort patents a machine in 1784. Cort's innovation is a furnace which shakes the molten iron so that air mingles with it. Oxygen combines with carbon in the metallic compond, leaving almost pure iron. Unlike the brittle pig iron (or cast iron), this purer metal is malleable. Capable of being hammered and shaped, it is a much more useful metal in industrial processes than cast iron.
One is the technique which becomes known as puddling, for which Cort patents a machine in 1784. Cort's innovation is a furnace which shakes the molten iron so that air mingles with it. Oxygen combines with carbon in the metallic compond, leaving almost pure iron. Unlike the brittle pig iron (or cast iron), this purer metal is malleable. Capable of being hammered and shaped, it is a much more useful metal in industrial processes than cast iron.
In the previous year Cort has also patented a machine for drawing out red-hot lumps of purefied metal between grooved rollers, turning them into manageable bars without the laborious process of hammering. His device is the origin of the rolling mills which subsequently become the standard factories of the steel industry.
Cort's subsequent career exemplifies the risks involved in the entrepreneurial excitements of the Industrial Revolution. After spending all his own money on his inventions, he raises further capital from the deputy-paymaster of the navy. It turns out to have been embezzled. Cort is ruined before his inventions bring him a profit.
Cort's subsequent career exemplifies the risks involved in the entrepreneurial excitements of the Industrial Revolution. After spending all his own money on his inventions, he raises further capital from the deputy-paymaster of the navy. It turns out to have been embezzled. Cort is ruined before his inventions bring him a profit.
This History is as yet incomplete.
Page
1
of
2